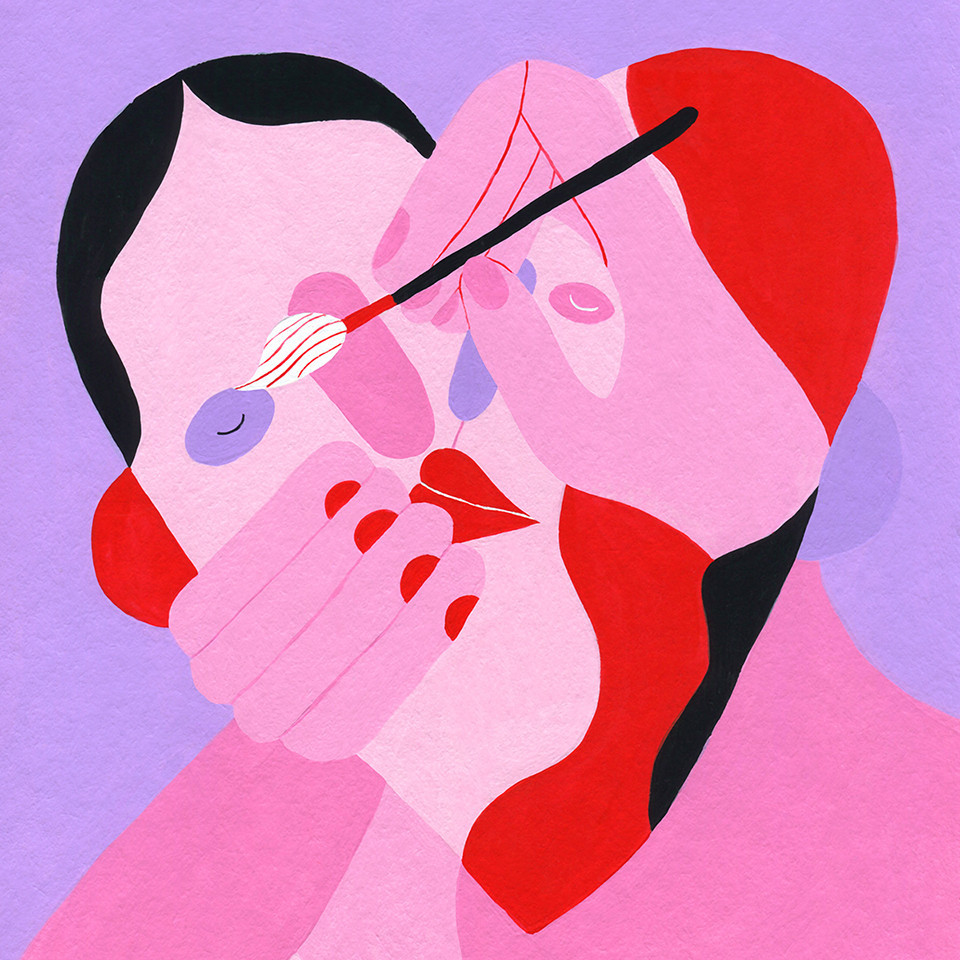
Meet the
makers
Interview and text by Laura Reinke, Photography by Maximilian Attila Bartsch
You need excellent denim in order to create excellent jeans – it’s as simple as that! We have been relying on Candiani’s high-quality denim for decades and almost every pair of Closed jeans has its origins in Candiani’s weaving mill in Robecchetto near Milan, where the world’s best cotton is transformed into yarn and woven into denim. Traditional craftsmanship and sustainable innovations – the Italian family business, founded in 1938, combines the best of both worlds. That is why Closed’s eco-denim line A BETTER BLUE was developed in close collaboration with Candiani.
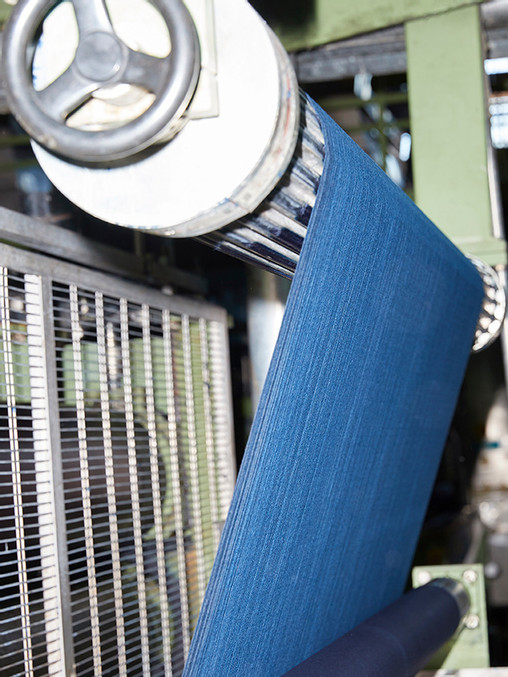
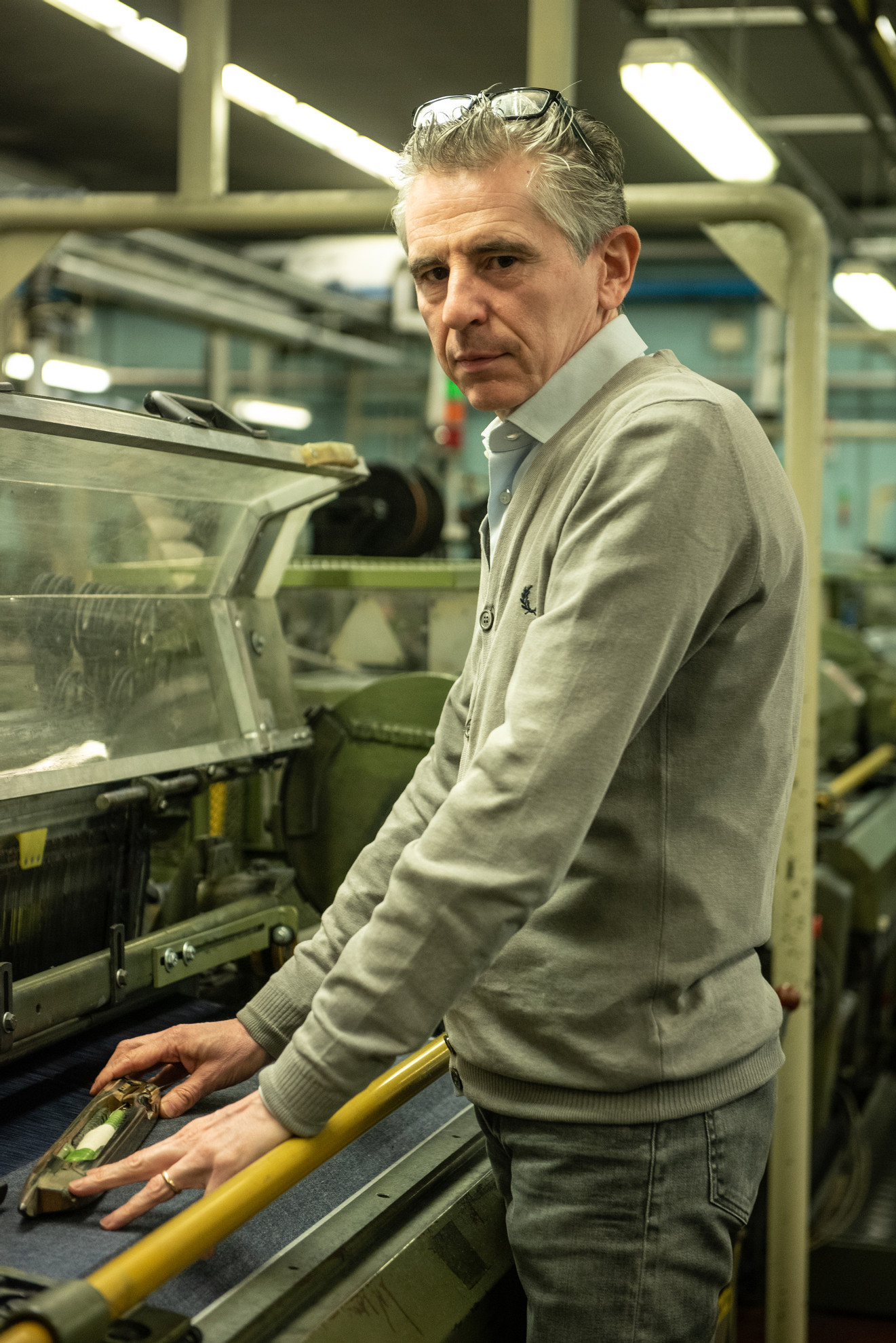
To learn more about the process of making denim, we talked to Luca Grimi, the manager of Candiani’s weaving department..
How denim is produced at Candiani, explained by Luca
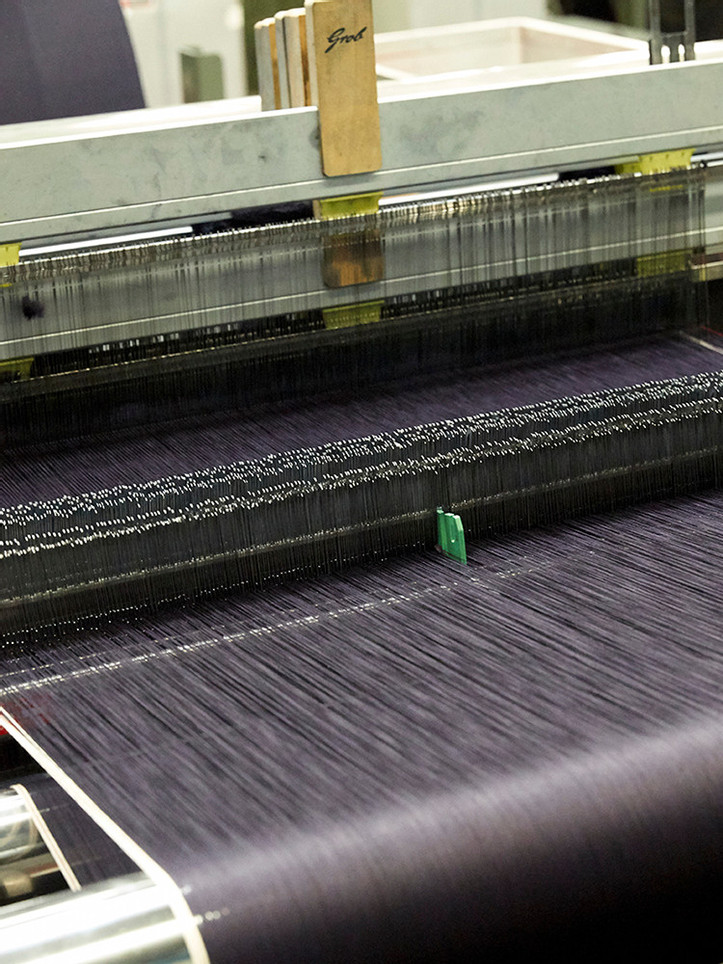
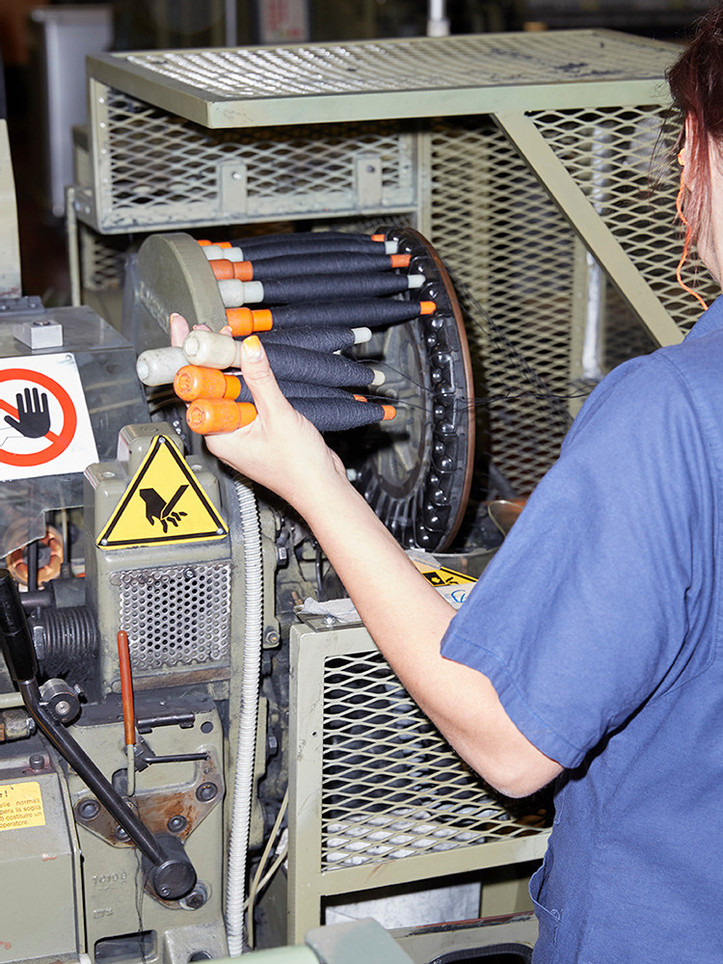
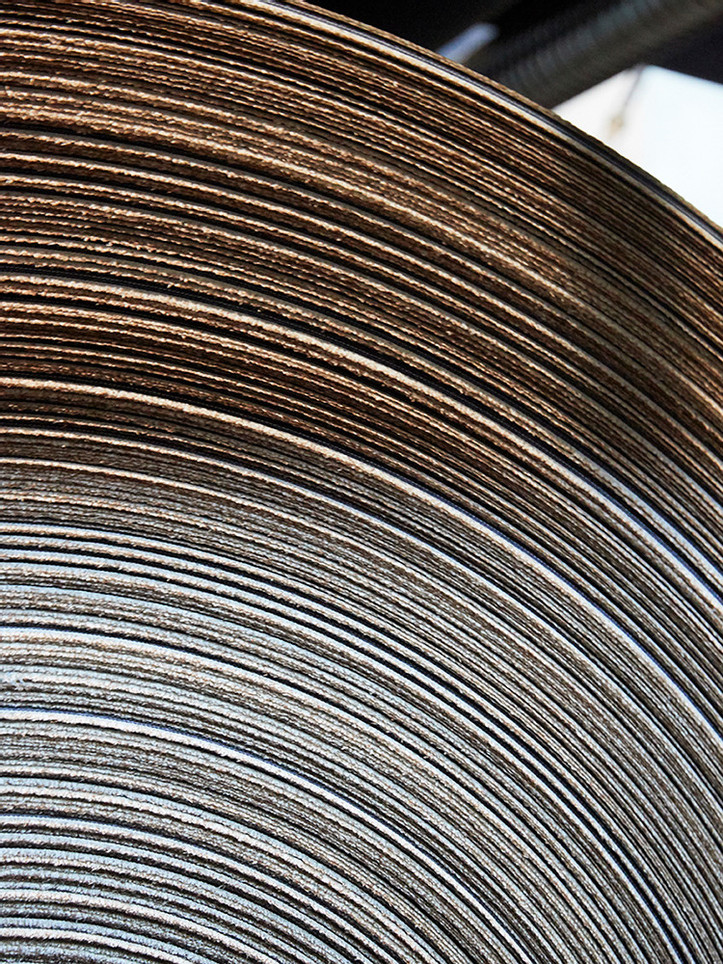
Interview and text by Laura Reinke, Photography by Maximilian Attila Bartsch
There is no winter season without knitted jumpers, cardigans and the like – and it all starts with soft wool yarns. Most of our high-quality yarns are spun in Italy, many of them in the traditional company Pecci Filati in Campi Bizensio, not far from Florence. Founded in 1884, Pecci Filati is one of the oldest yarn producers in the Prato region, which is known worldwide for traditional textile production. Using different raw materials – from alpaca wool to merino and cashmere – Pecci Filati creates yarns with different structures, always in particularly bright, rich colours. Every season, Pecci Filati’s experts come up with new finishes and colours. For the yarn we use for our knitwear, the skilled employees often develop individual compositions especially for us. Every type of yarn is refined bit by bit until it’s absolutely perfect.
Pecci Filati pays a lot of attention to sustainability. The company has many certifications (GOTS, Global Recycle Standard, Responsible Wool Standard, Responsible Alpaca Standard, etc.) and has for many years been committed to offering products that guarantee total traceability of the entire production process. This doesn’t only take into account animal welfare and the conservation of the land, but also using recycled materials and eliminating hazardous substances from the production cycle.
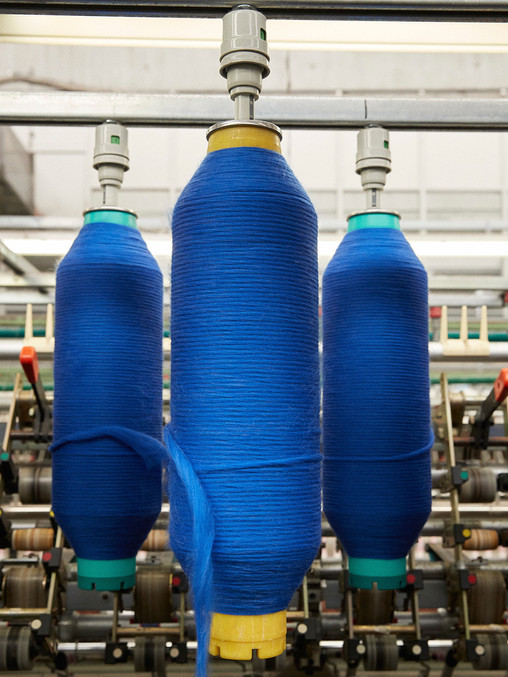
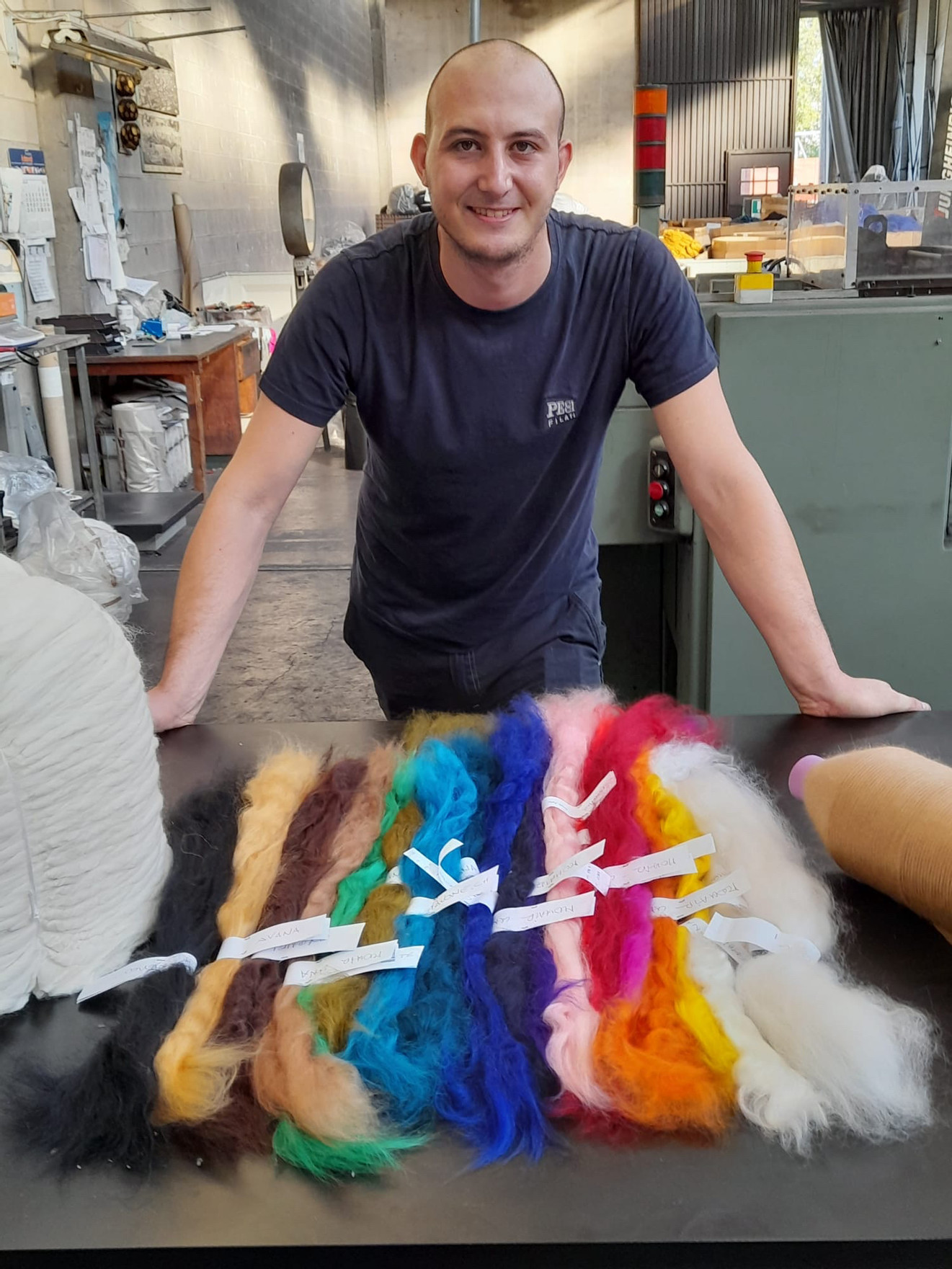
We talked about the process of creating high-quality yarns with Alessio Marini who joined the company in May 2021. He took the position of Pecci Filati’s previous technician Riccardo Coppini, who retired after more than 40 years with the company.
How yarn for our Closed knitwear is made, explained by Alessio
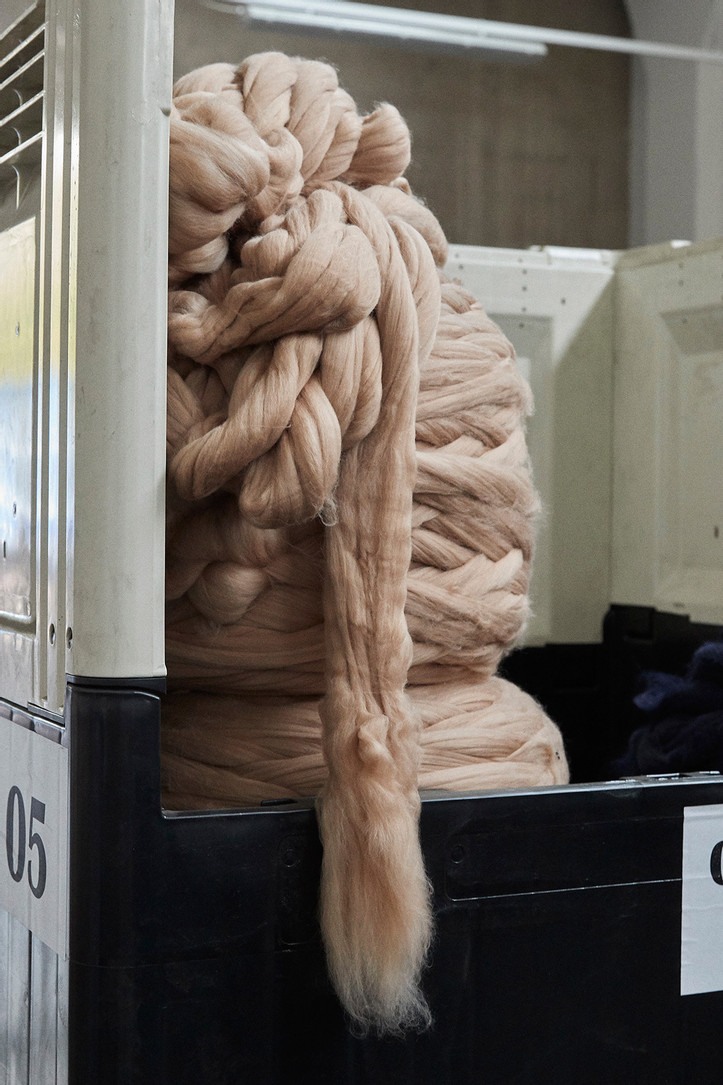
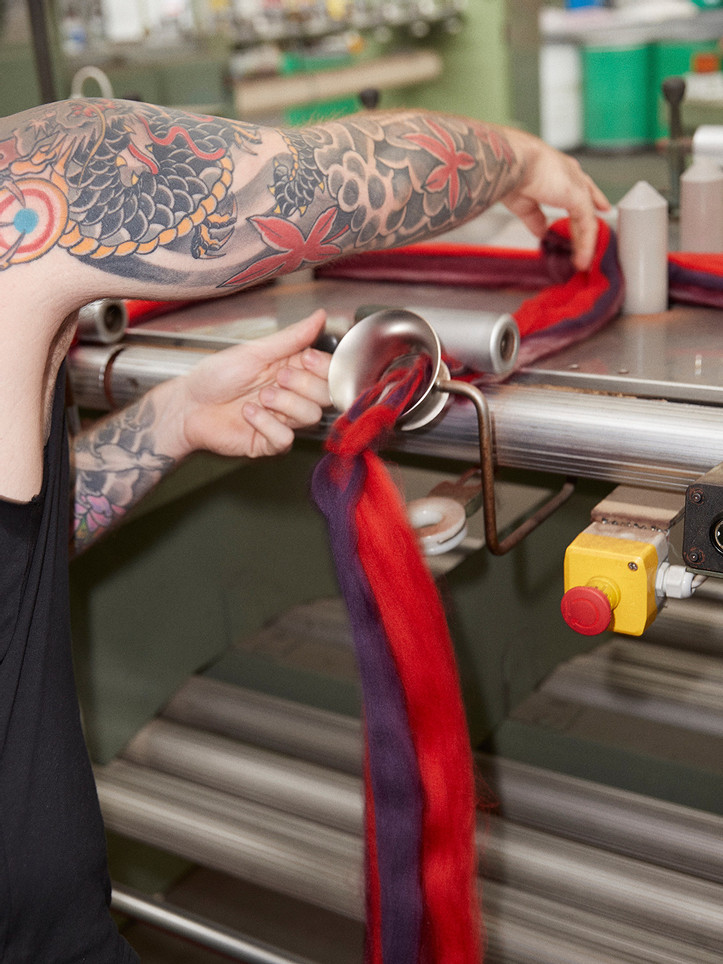
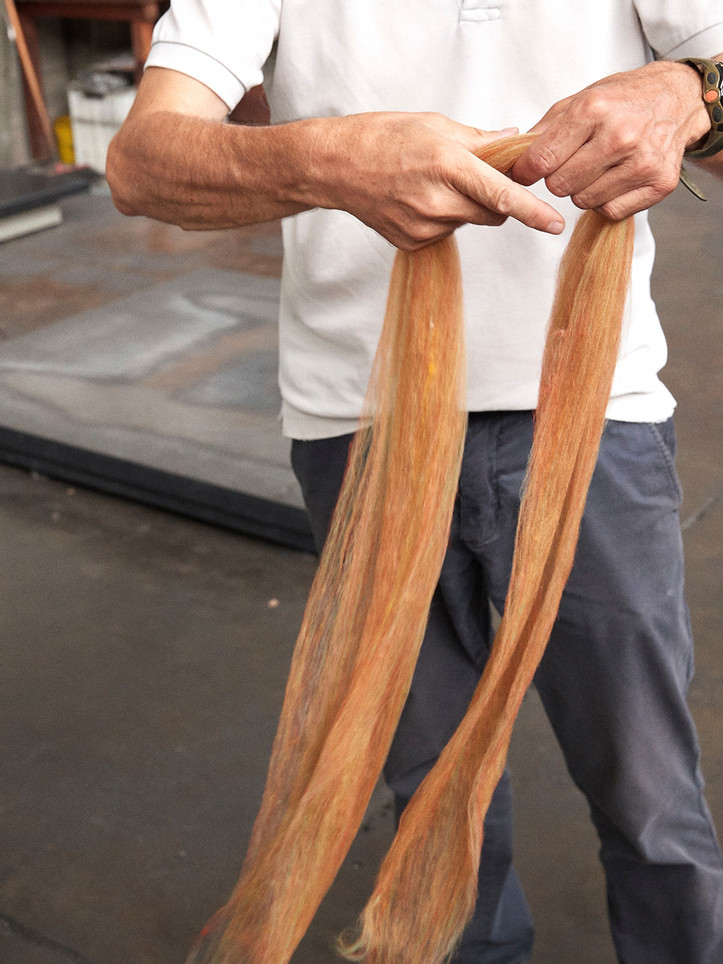
Interview and text by Laura Reinke, Photography by Maximilian Attila Bartsch
It’s all about the perfect essentials. To create the perfect T-shirts for every day, we have been trusting in the expertise of our jersey specialists Caifai for almost 15 years. The family business, located in the northern Portuguese town of Barcelos, was founded in 1987 by the married couple Conceição and David Simões. At Caifai, our designs are implemented with the help of state-of-the-art CAD/CAM software, which guarantees particularly precise planning and thereby keeps material waste to a minimum. Every finished garment undergoes a quality control check and is carefully ironed and packed by hand – so that it arrives at its destination in perfect condition. Caifai is a real family business. Two generations and their relatives are at the helm of the company today. In order to support the constantly growing business, the son of the founders, André Simões, even hung up his doctor’s coat and is now working in Caifai’s management.
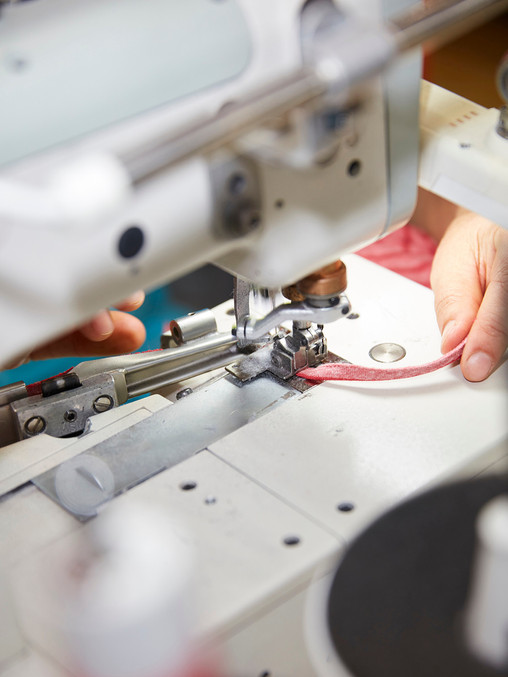
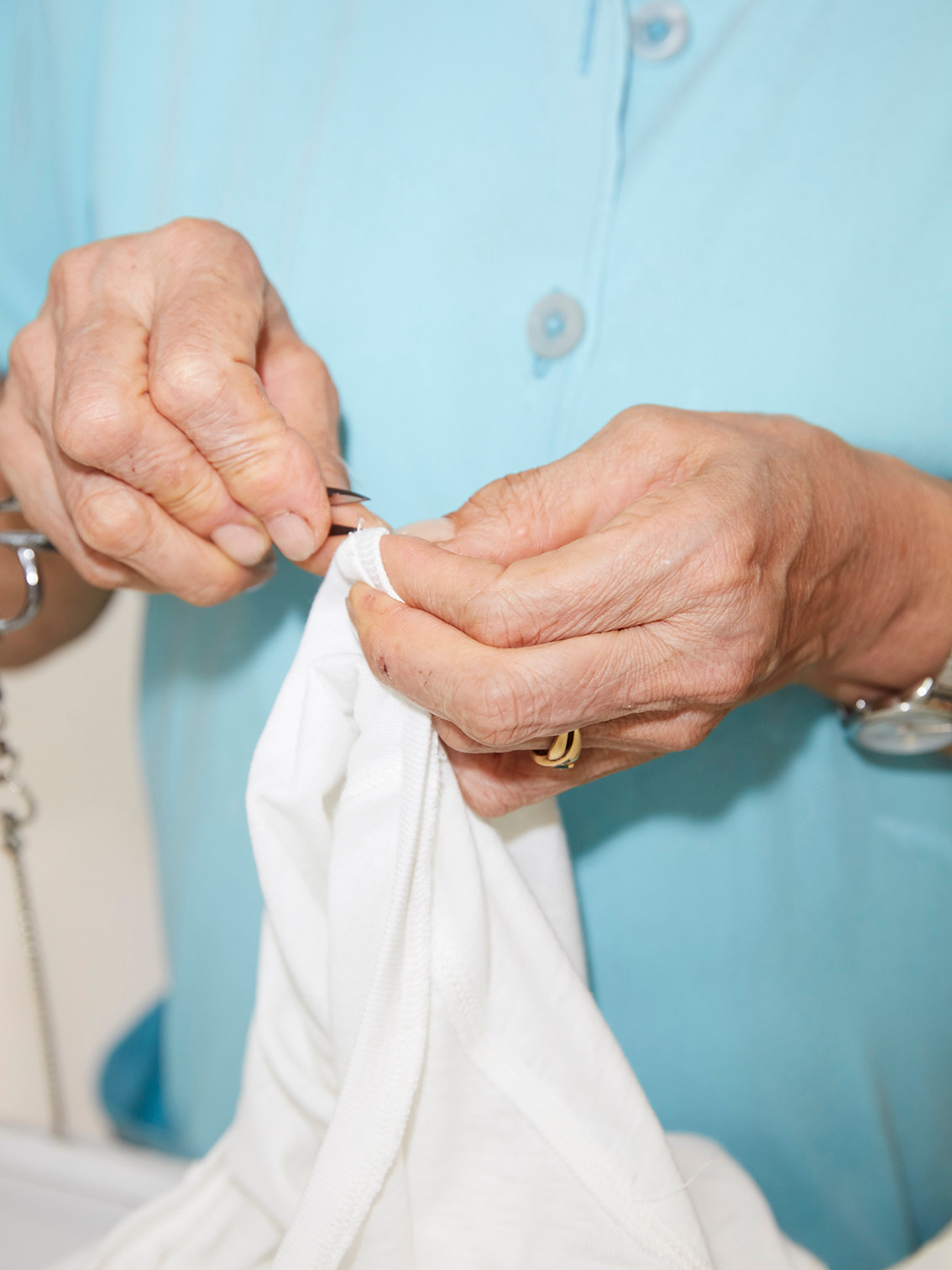
We talked to staff member Patricia about working at Caifai – and she explains the process of producing a typical Closed T-shirt.
How a Closed T-shirt is made, explained by Patricia
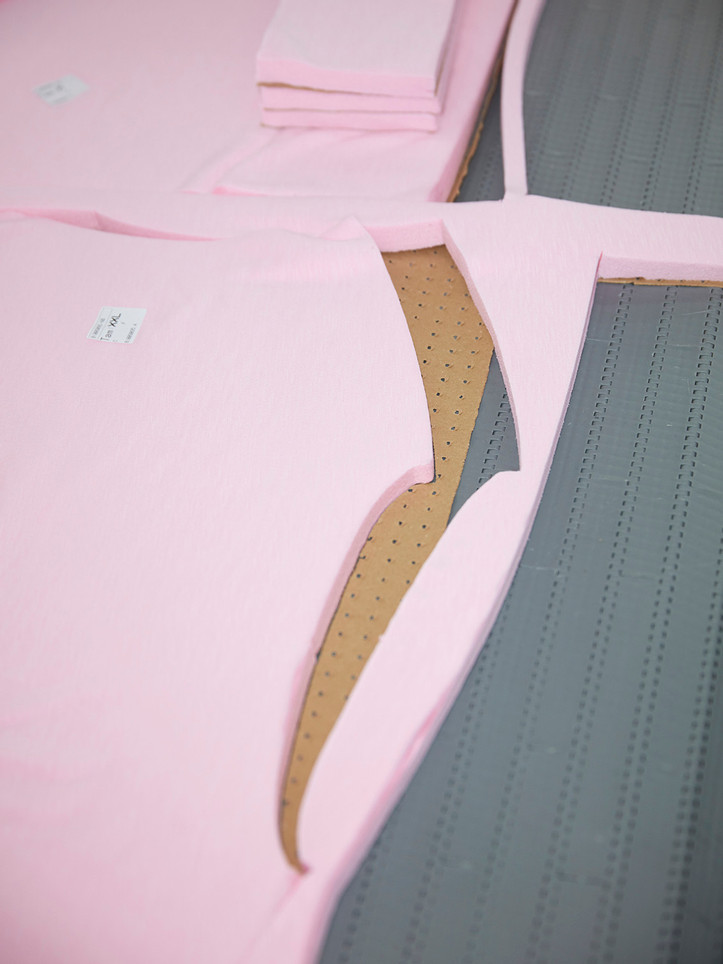
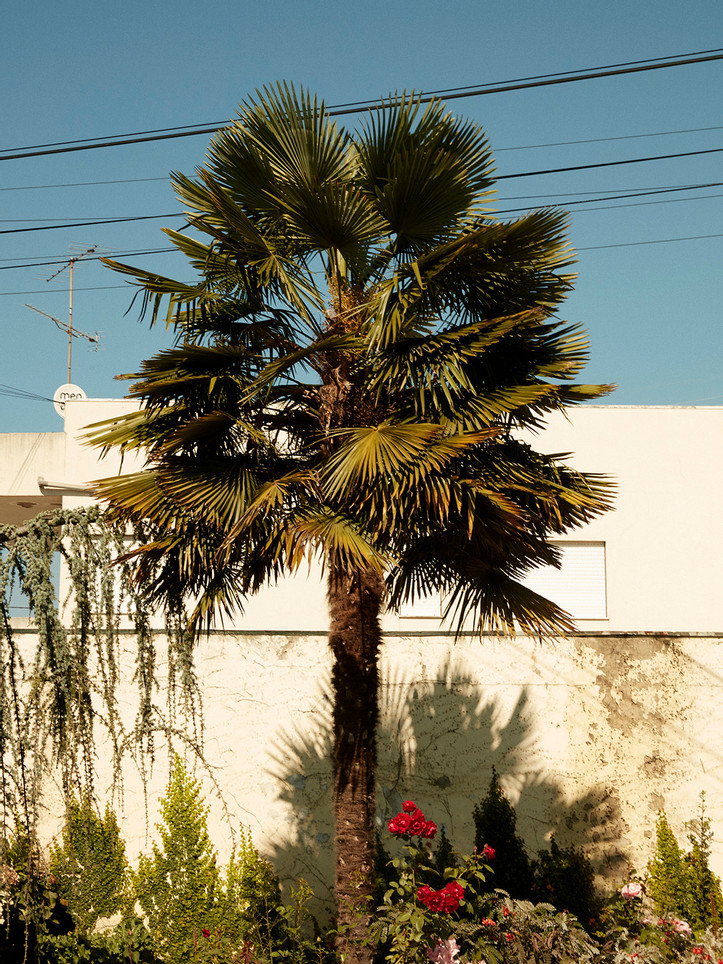
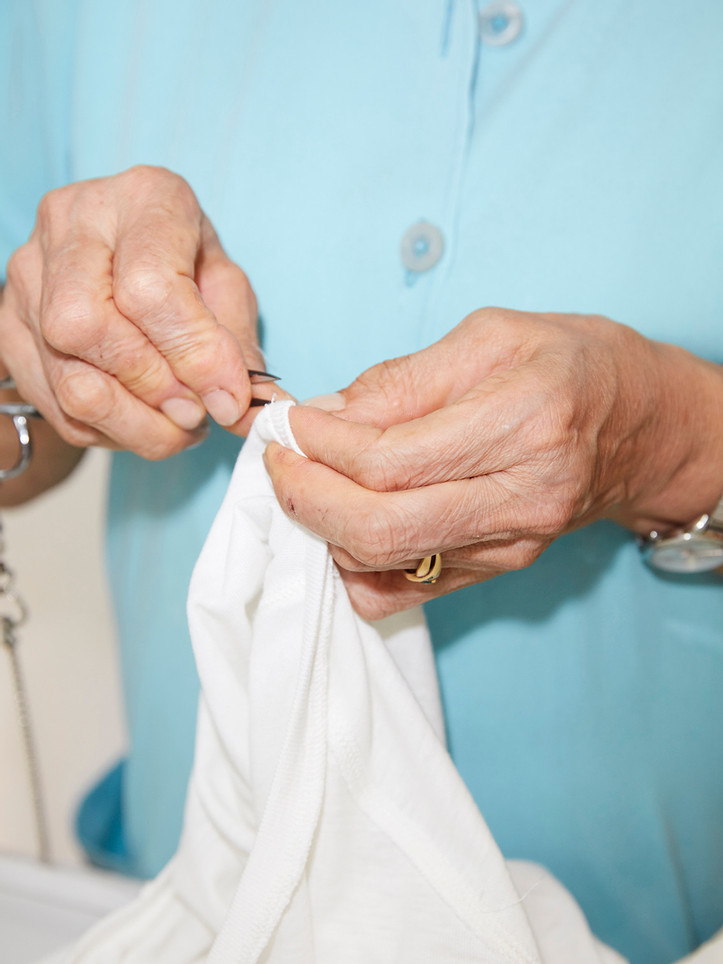
Interview and text by Laura Reinke, Photography by Maximilian Attila Bartsch
Our blazers and jackets are made in Romania by the company Texdata in Focsani. Texdata is our specialist for ready-to-wear garments – from coats to skirts and pants – and we love their attention to detail and high level of innovation. Texdata uses the latest technology to create high-quality garments. The company – our partner for eleven years – has even developed its own ironing press for our Closed blazers and constantly comes up with new ideas and techniques for special workmanship, including the double-face we developed and perfected together. The company experimented for a long time and invested in new machines to make our vision of high-quality double-face garments possible. Although Texdata is very modern and innovative, the atmosphere feels like a big family. Many of Texdata’s 160 employees have been with the company for a long time – and several of them share their workplace with a spouse or relative.
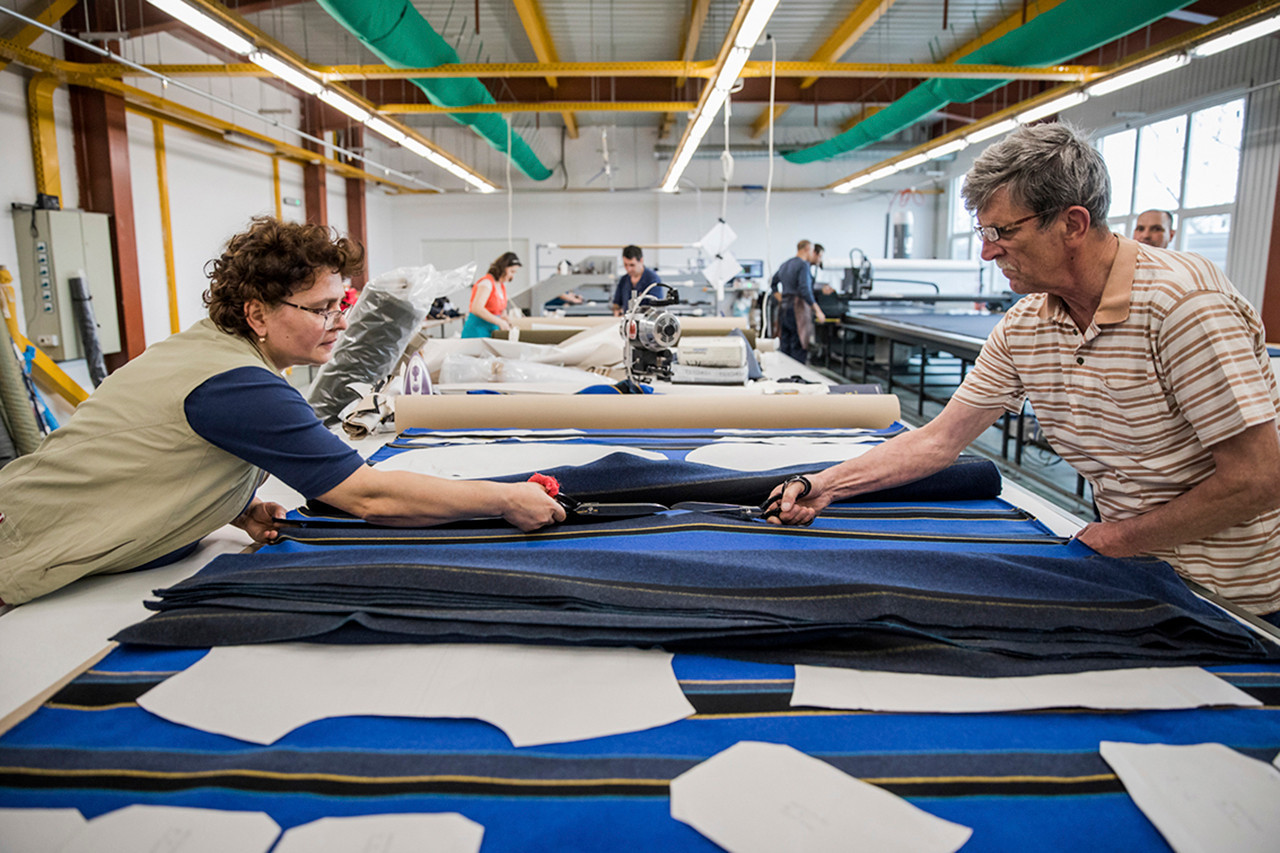
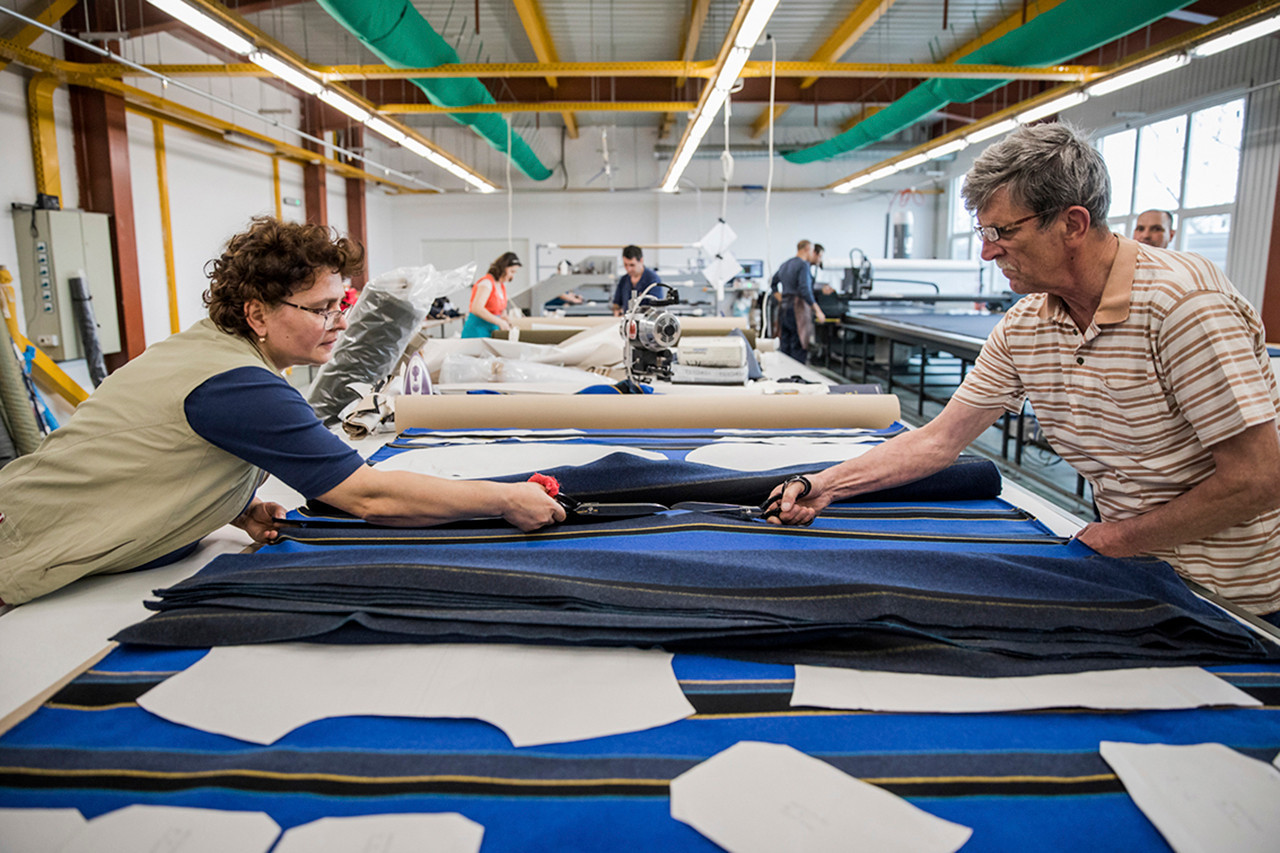
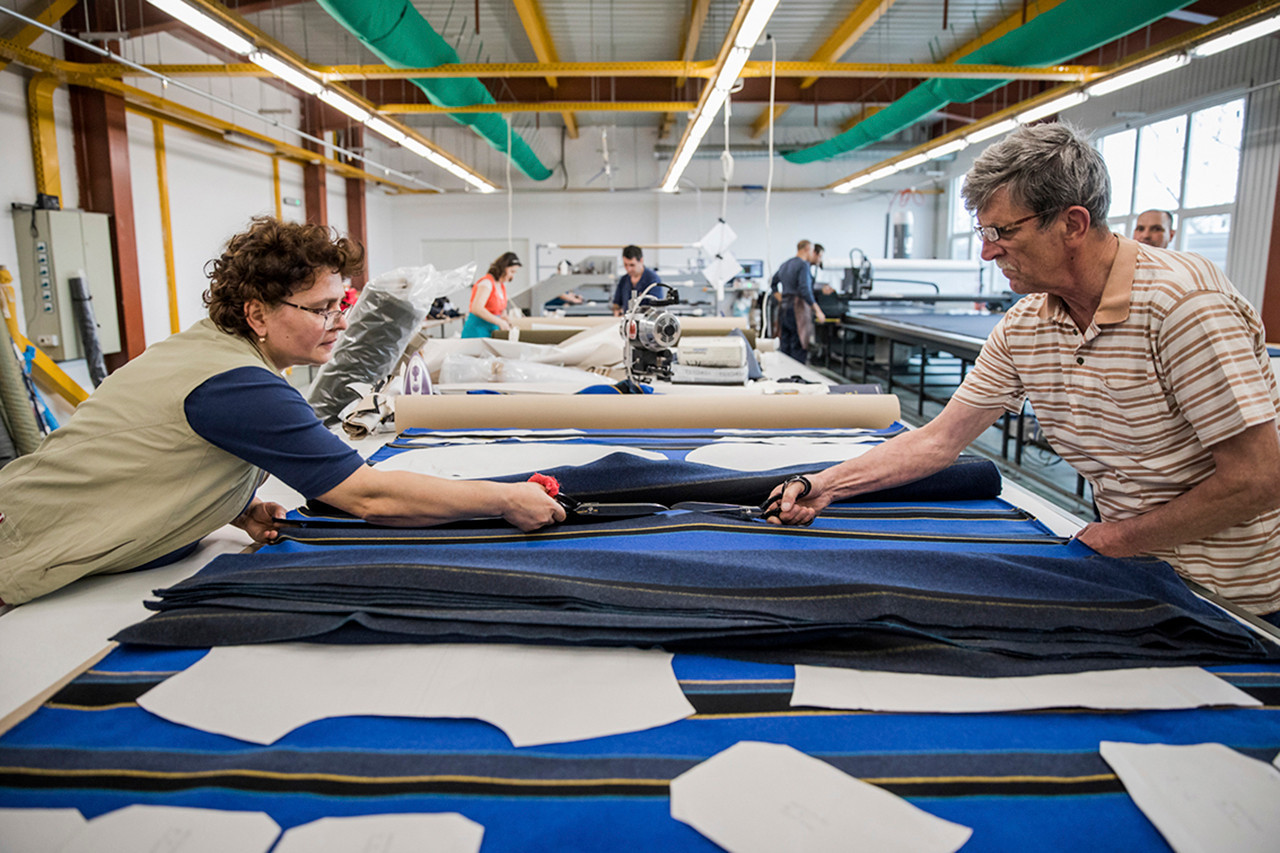
We spoke to Oana Ploscaru, chief of technological processes and part of the Texdata team for seventeen years, about her work.
How a Closed blazer is made –
step by step
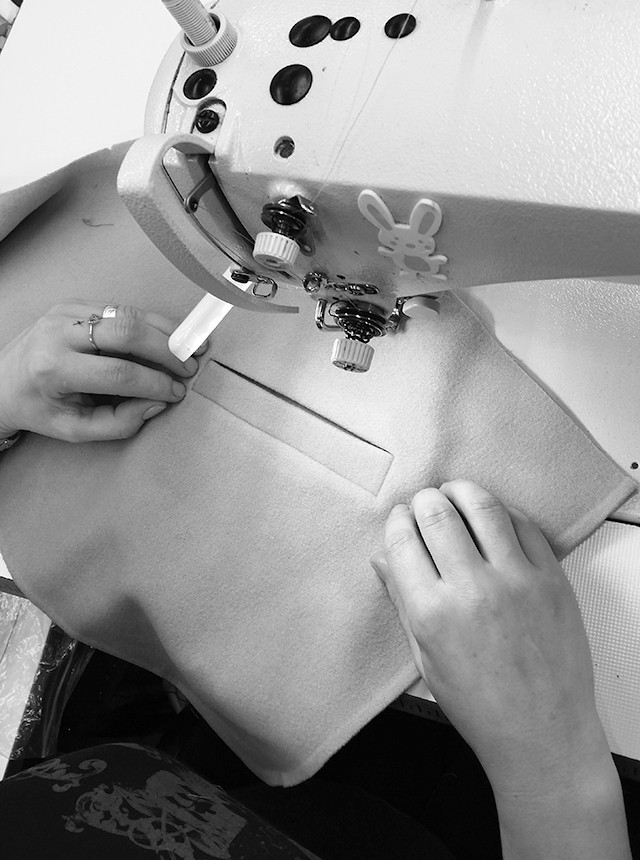
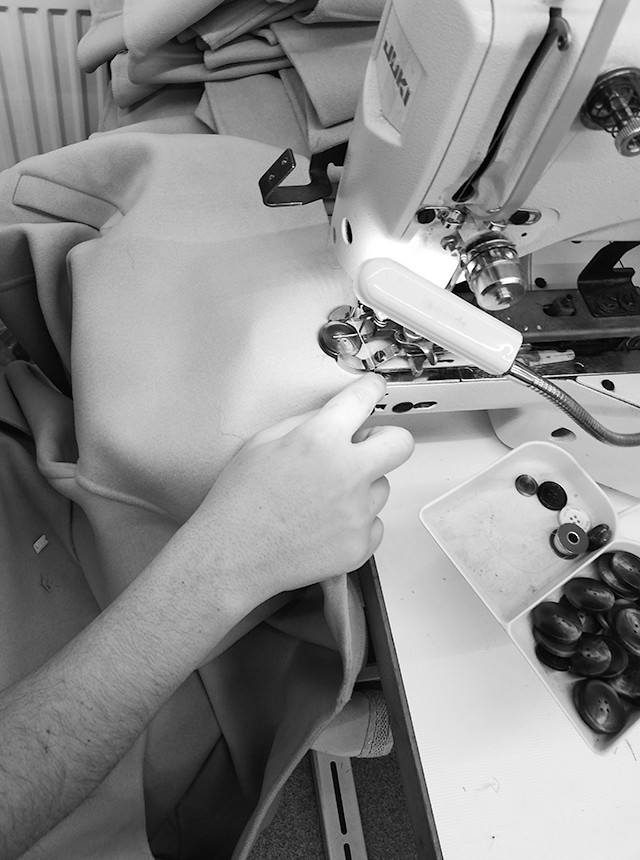
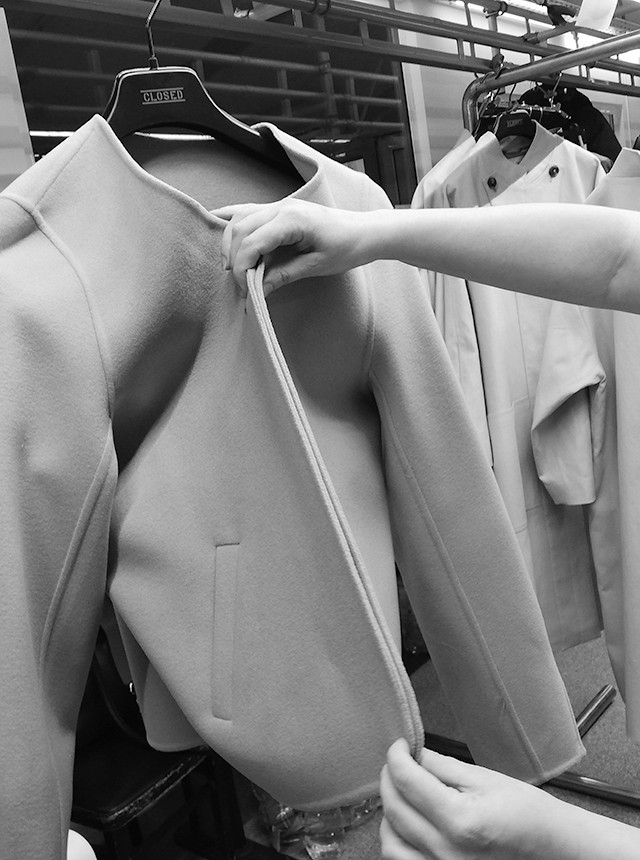
Interview and text by Laura Reinke, Photography by Maximilian Attila Bartsch
The La Doma tannery in Spain treats the high-quality lambskin for our shearling coats and jackets. Tanning is a traditional technique that requires a lot of knowledge – the more so when it comes to double-sided lambskin, La Doma’s speciality. The company has two divisions: the skins are prepared and tanned in Barbastro, then dyed and finished in Centelles near Barcelona.
Founded in 1985, La Doma has continually grown. The headquarters in Centelles grew, too, with the addition of several extensions, which explain the building’s unique character with many staircases and corridors that can feel like a labyrinth. Peter Colomer, who comes from a family of tanners, manages the company with 164 employees.
La Doma combines tradition and innovation: the tannery uses eco-friendly, water-saving techniques and has a repair shop to fix rather than replace machines. When La Doma has finished the skins, they are shipped to our shearling expert Otto in Turkey who creates our garments with them. By the way, all the lambskins La Doma processes are by-products of the food industry.
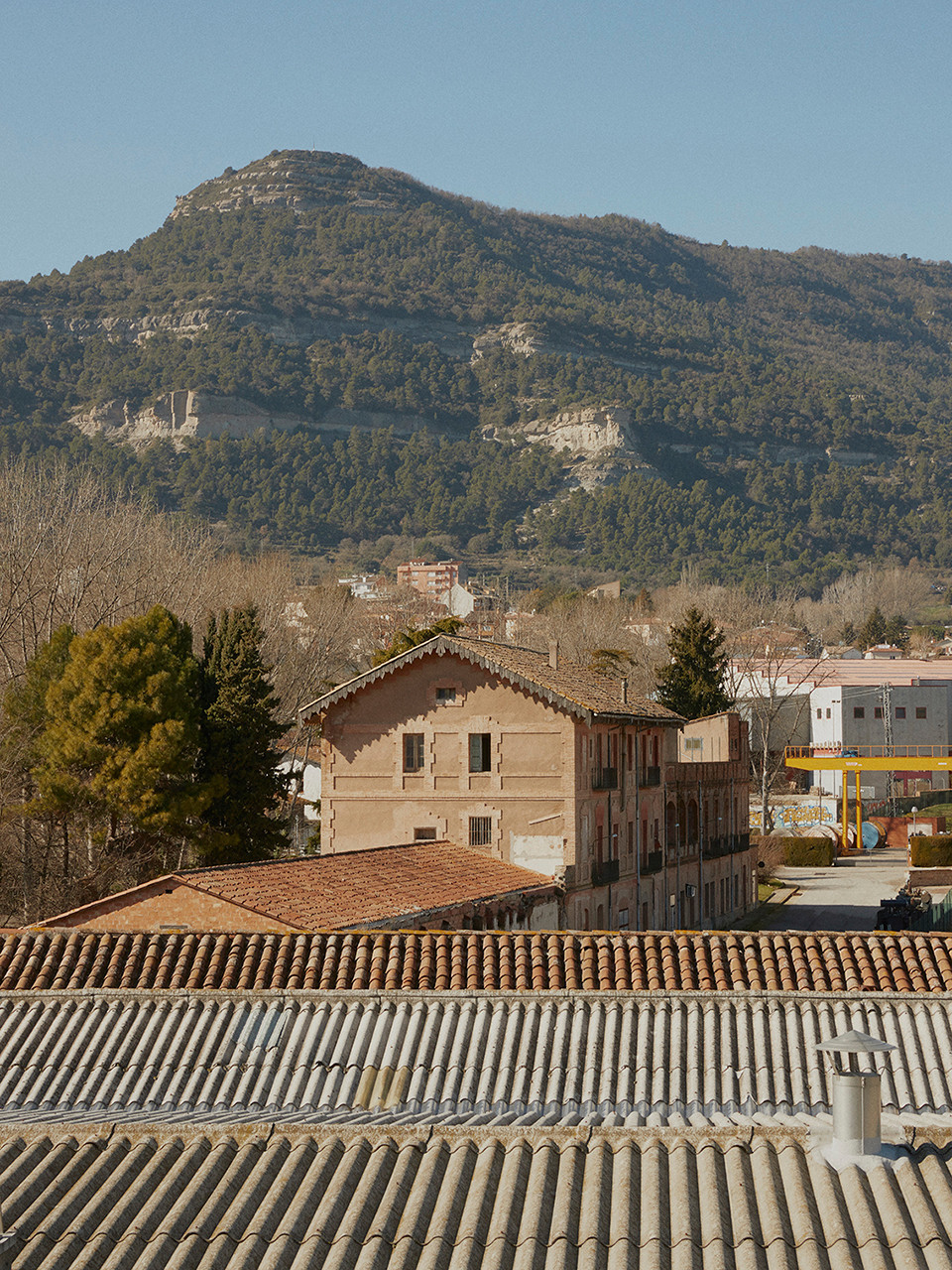
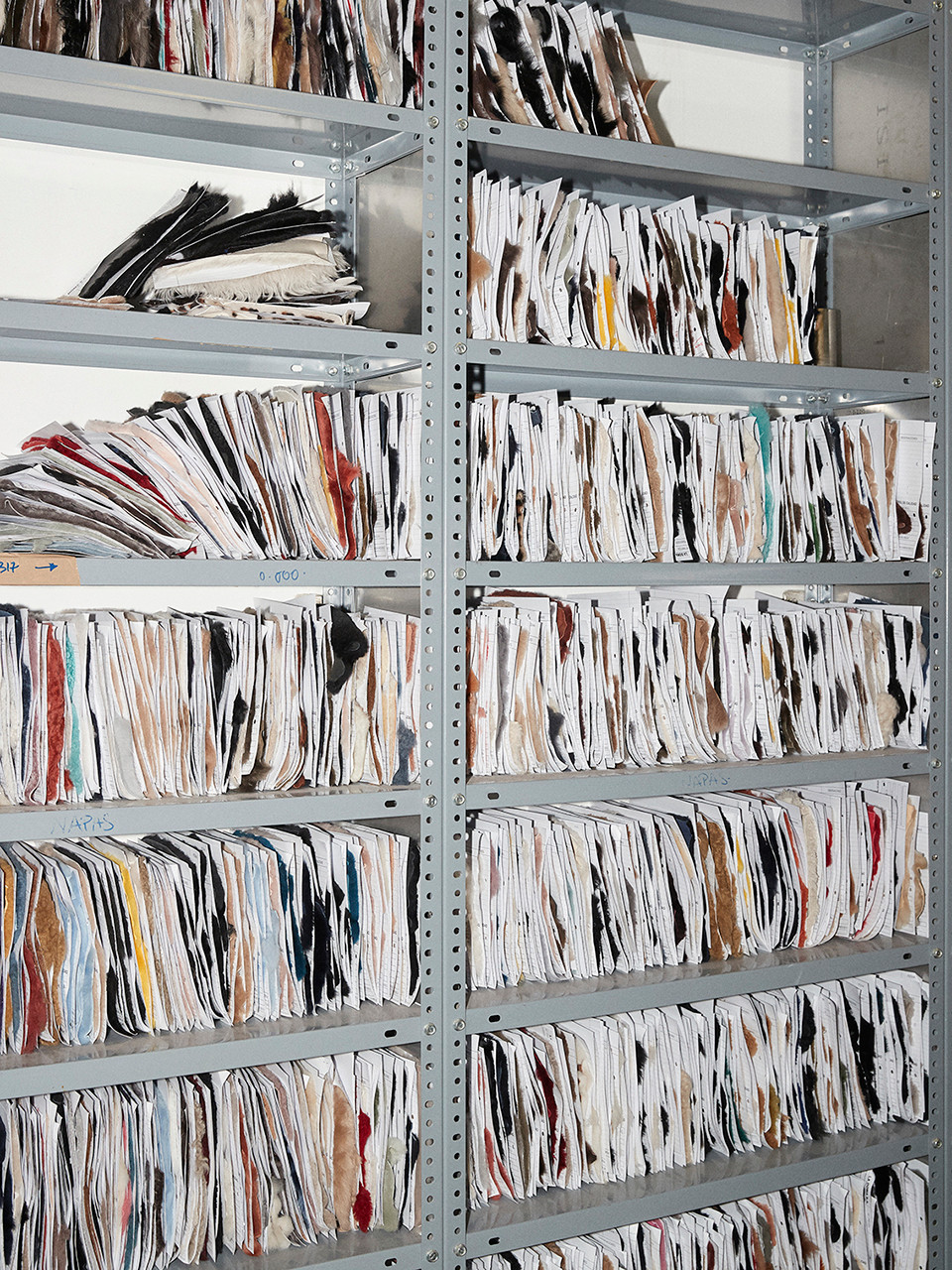
We talked to Elvira Fatjo, creative director and Peter’s wife, about her work. She joined La Doma 24 years ago.
The tanning and dyeing process –
step by step
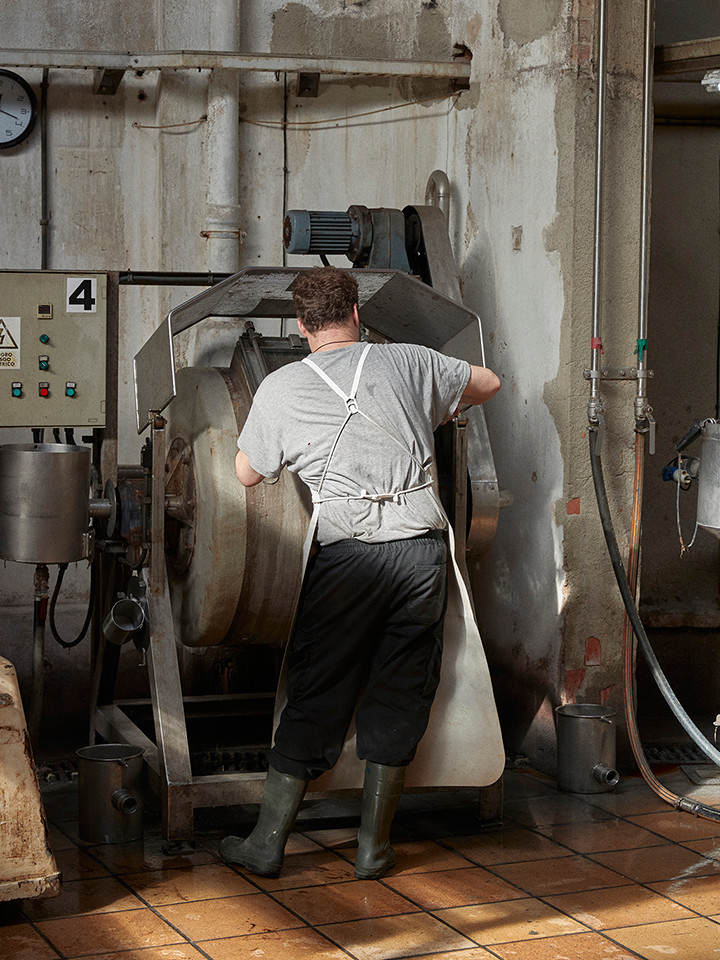
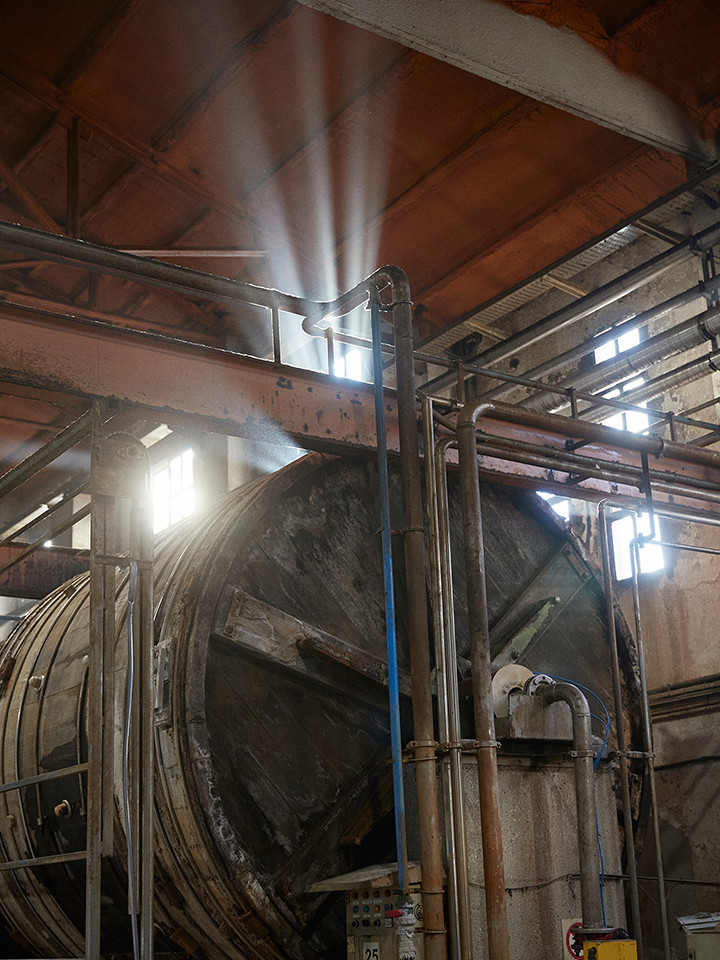
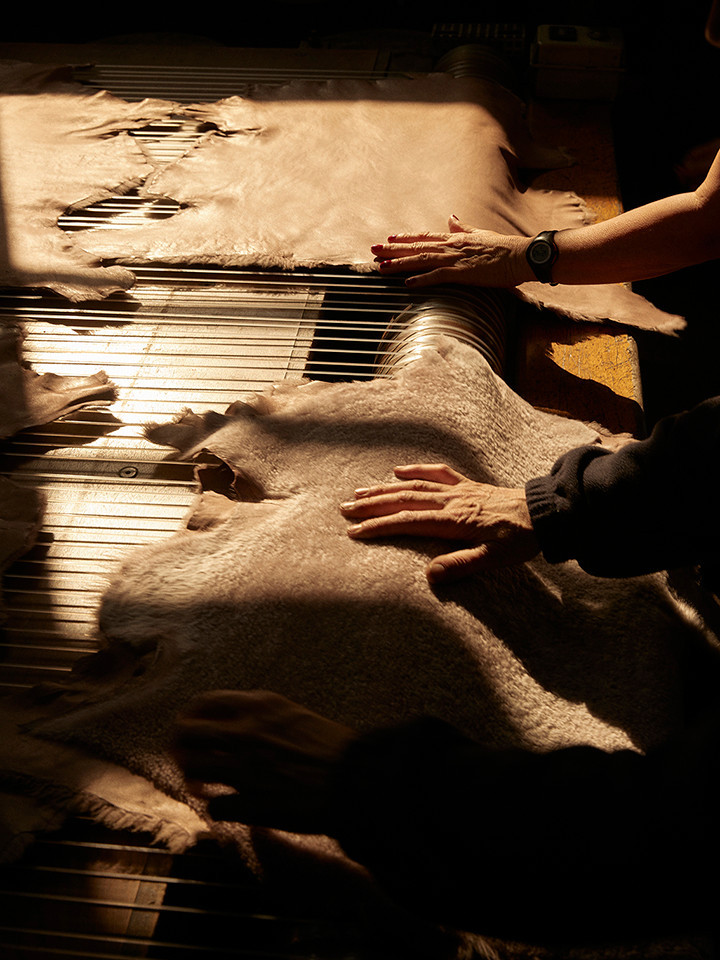
Interview and text by Laura Reinke, Photography by Maximilian Attila Bartsch
Most of our cotton shirts and blouses are made in Portugal, at the Mundicorte factory in São Martinho do Campo, 45 minutes from Porto. The motto of Agostinho Pereira and José Almeida who founded Mundicorte in the Eighties: “Profession and Passion”!
The company started as a small family business with the intention of creating high-quality men’s shirts. Gradually, Mundicorte grew bigger and bigger – and now, around 200 employees also produce women’s shirts and blouses, dresses, jumpsuits, trousers and Bermudas. Of course, everything is done with respect for the environment and the same high quality standards and artisanal processes as back in the company’s early days. Up to 800 garments are finished per day, often using Portuguese organic cotton qualities – from crisp poplin to sturdy Oxford fabrics.
Now in the second generation, Mundicorte is headed by Agostinho Pereira’s son Filipe Martins. Some of his cousins and an aunt also work in the company, his mother is now retired after many years at Mundicorte. It’s still a family business! And, related or not, many of the highly-skilled specialists have been with the company for decades, from apprenticeship to retirement. Oh, and chef Glória has been cooking for the team since 1987 – a healthy soup with fresh vegetables for lunch, every day.
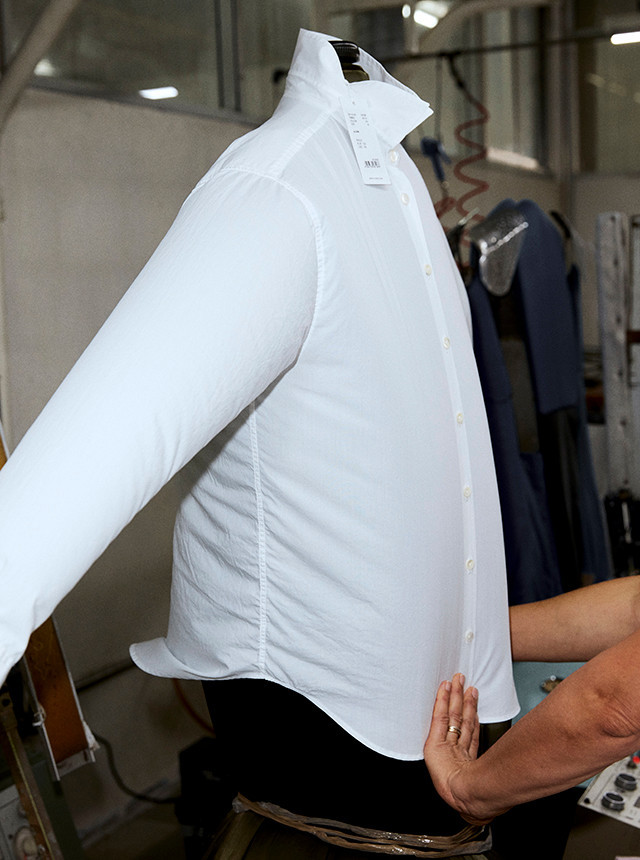
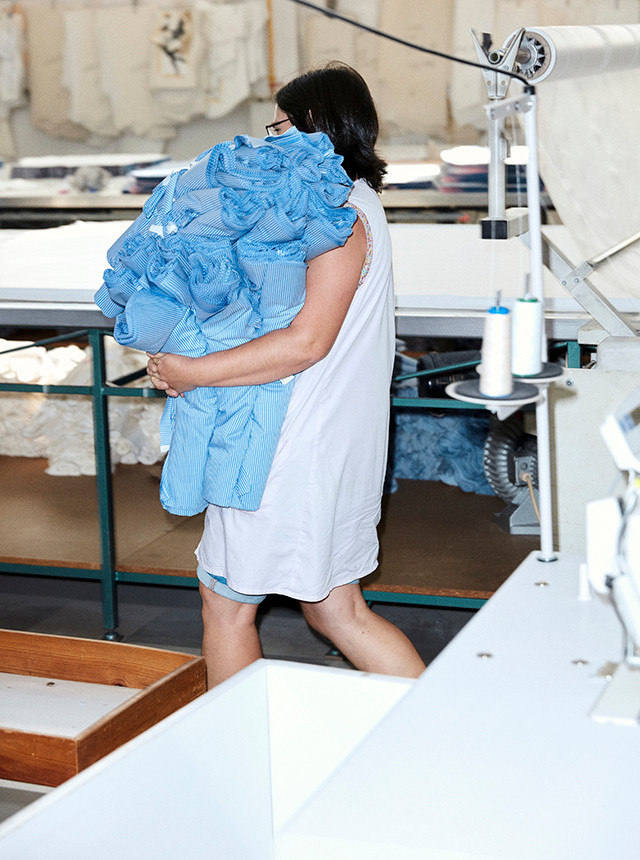
We asked Filipe Martins a few questions – and he explains how a classic Closed shirt is made, step by step.
How a Closed shirt is made –
step by step
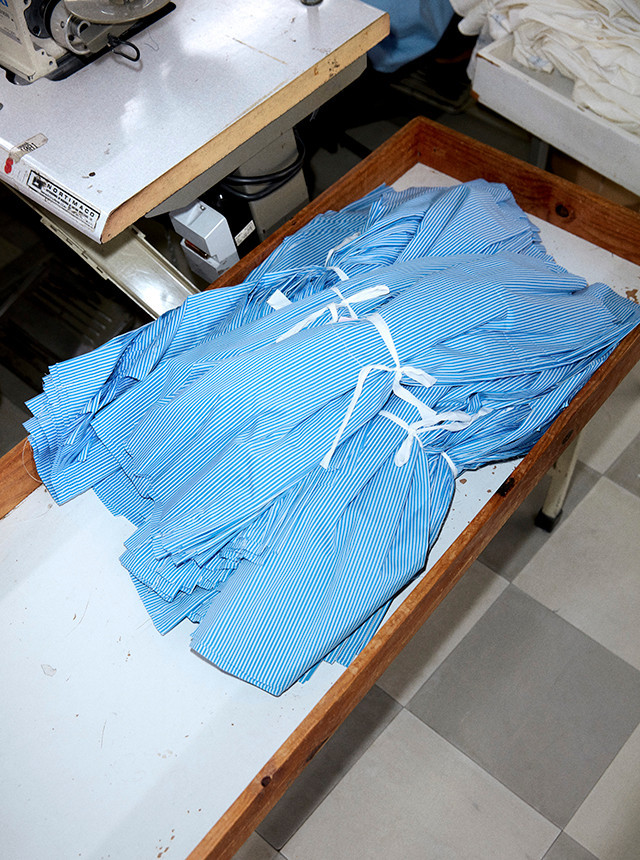
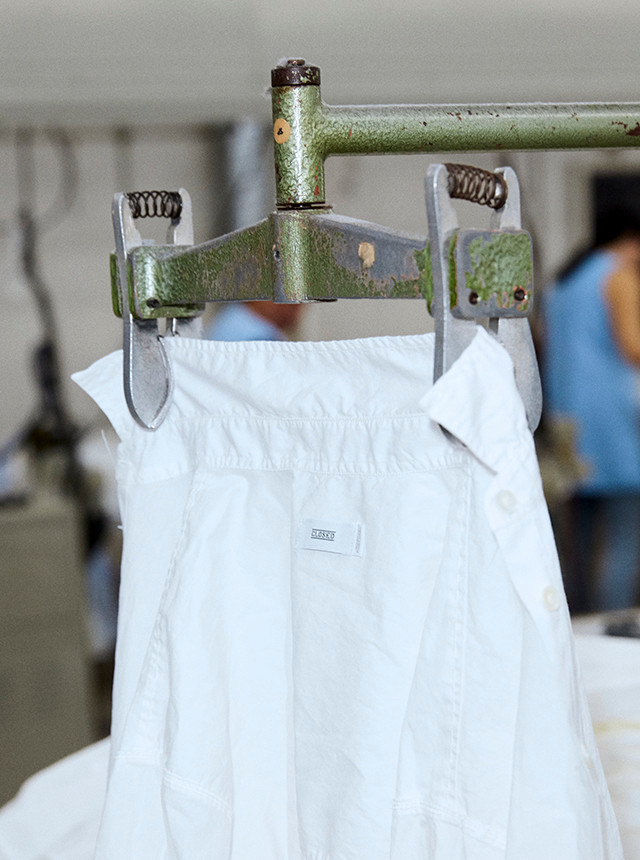
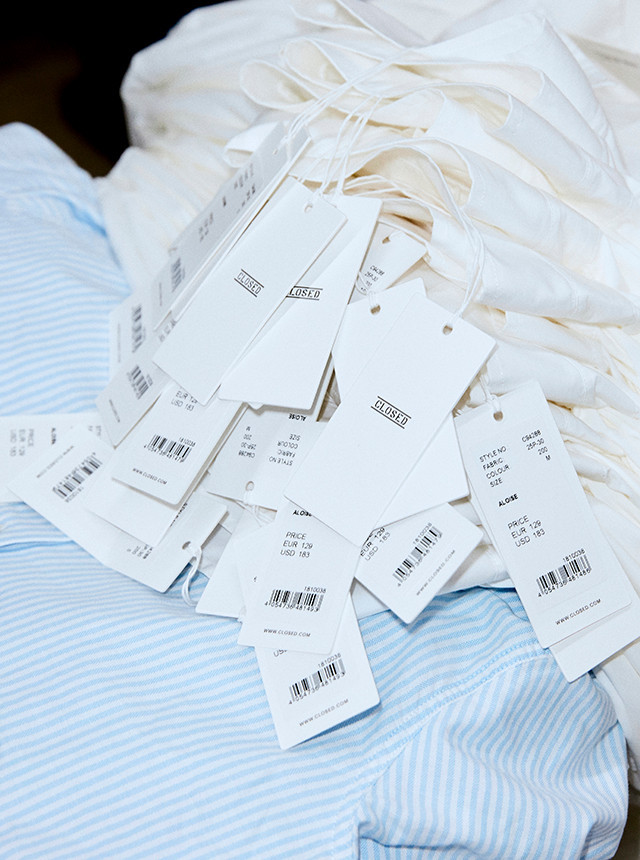
Interview by Giulia Stanzione, Text by Laura Reinke, Photography by Maximilian Attila Bartsch
For over thirty years, Cinturificio G. & G. has been our specialist for the finest-quality belts. The 7-person Italian belt maker is a real family company: alongside company founder Giulio Gastaldello, his wife Carla Gesuato and their children Alessandra and Enrico all work at Cinturificio G. & G. in Saletto di Vigodarzere near Padua. Each belt is made of fine Italian leather and is crafted almost entirely by hand – from cutting to punching and smoothing. Everyone at the factory shares an incredible love for detail and it shows in the beautiful, durable products they produce.
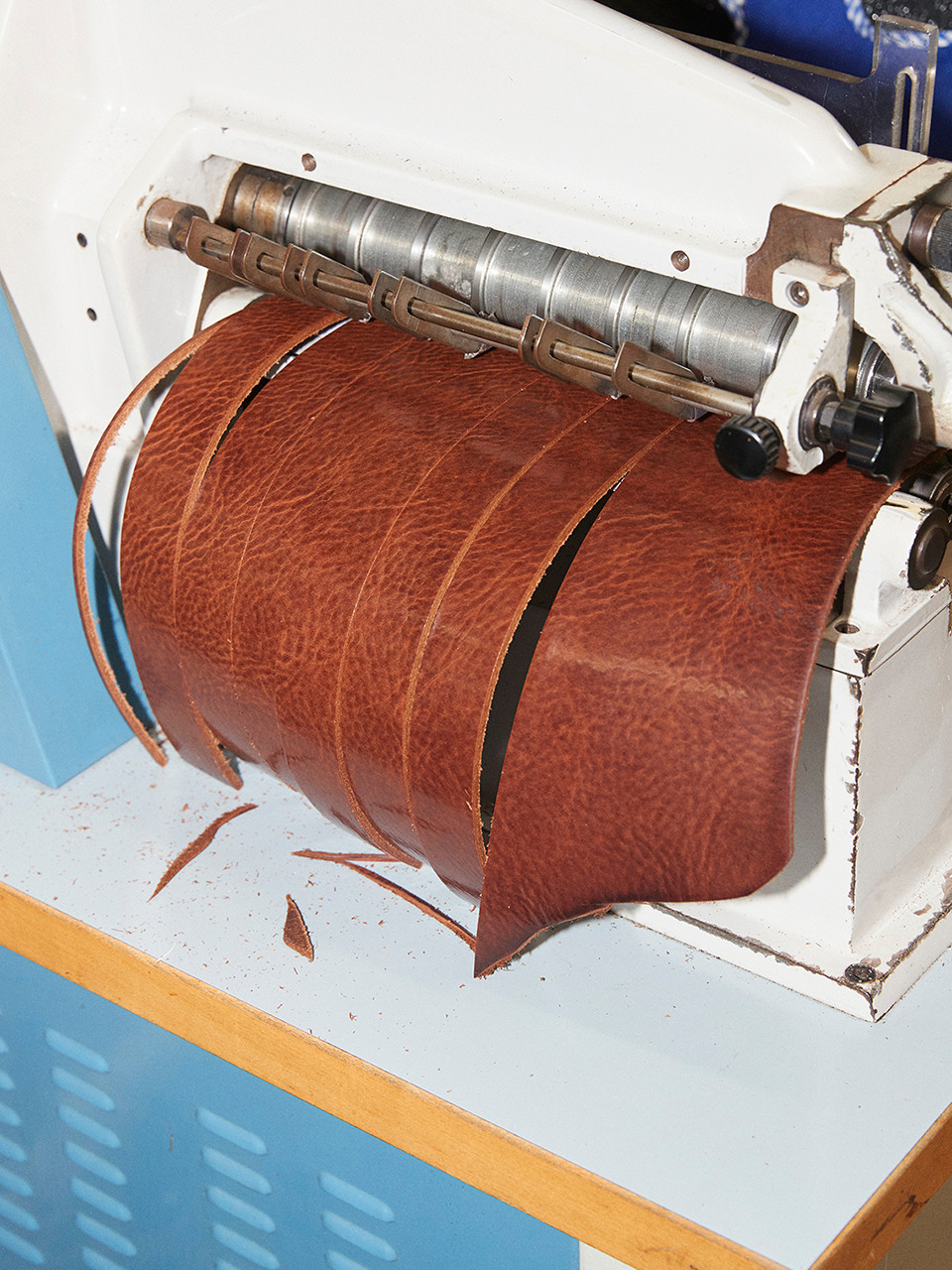
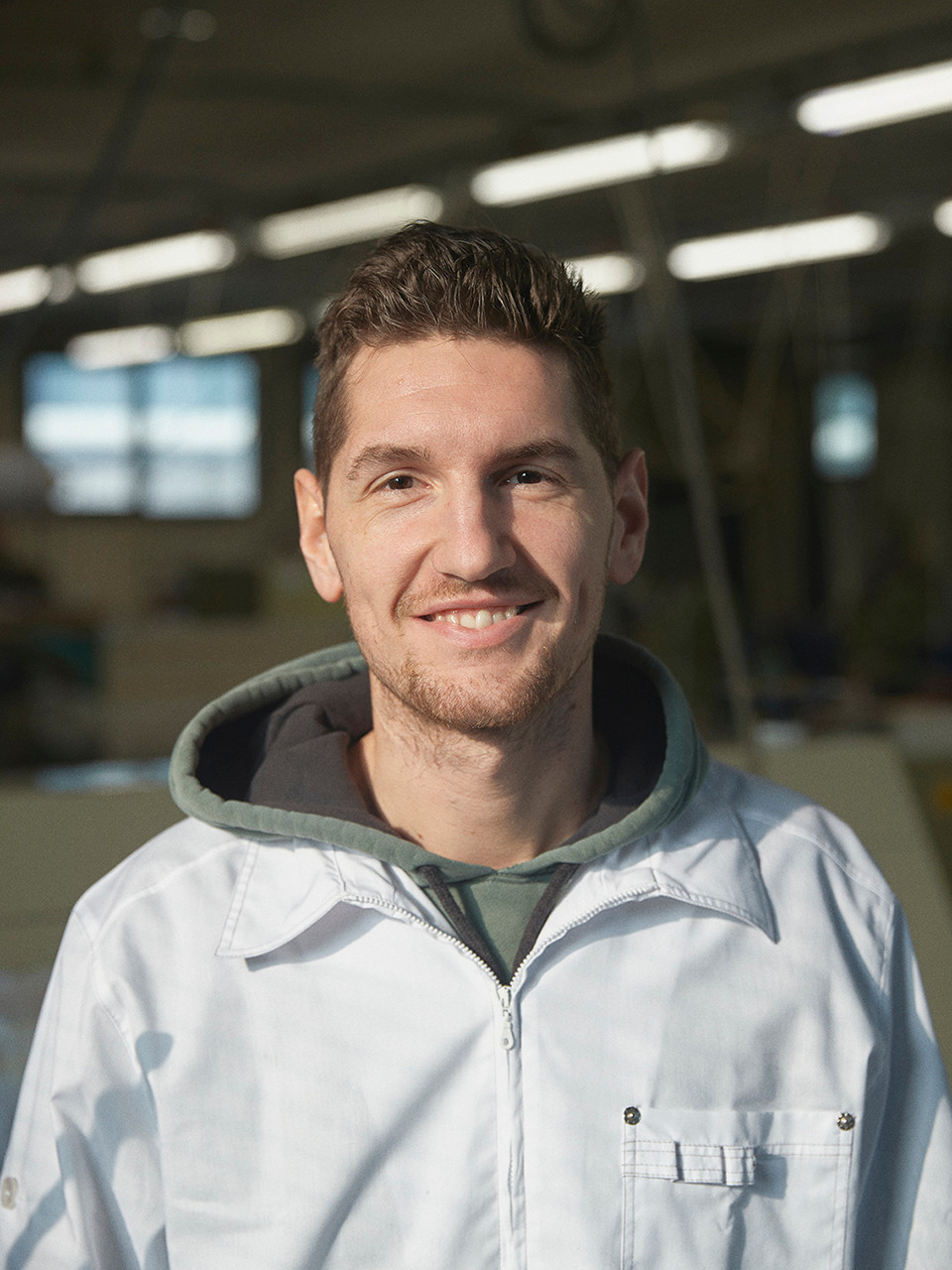
Enrico Gastaldello has a masterful command of most steps of the process and, unless he happens to be wearing sweatpants, he unfailingly wears a belt. We chatted to him and found out more about the art of making belts.
How a belt is made –
step by step
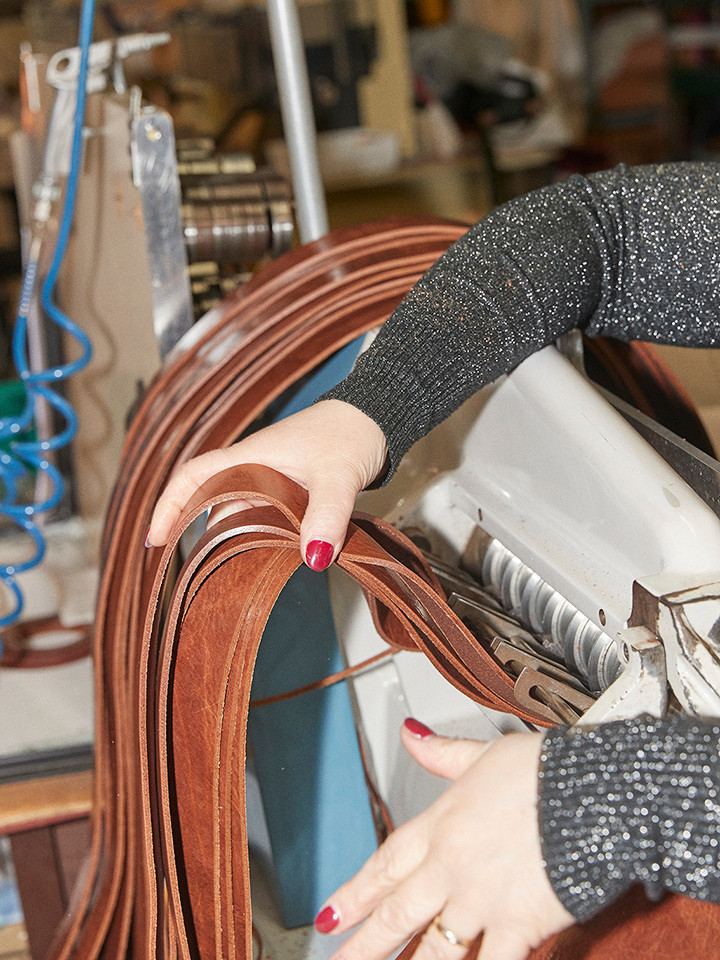
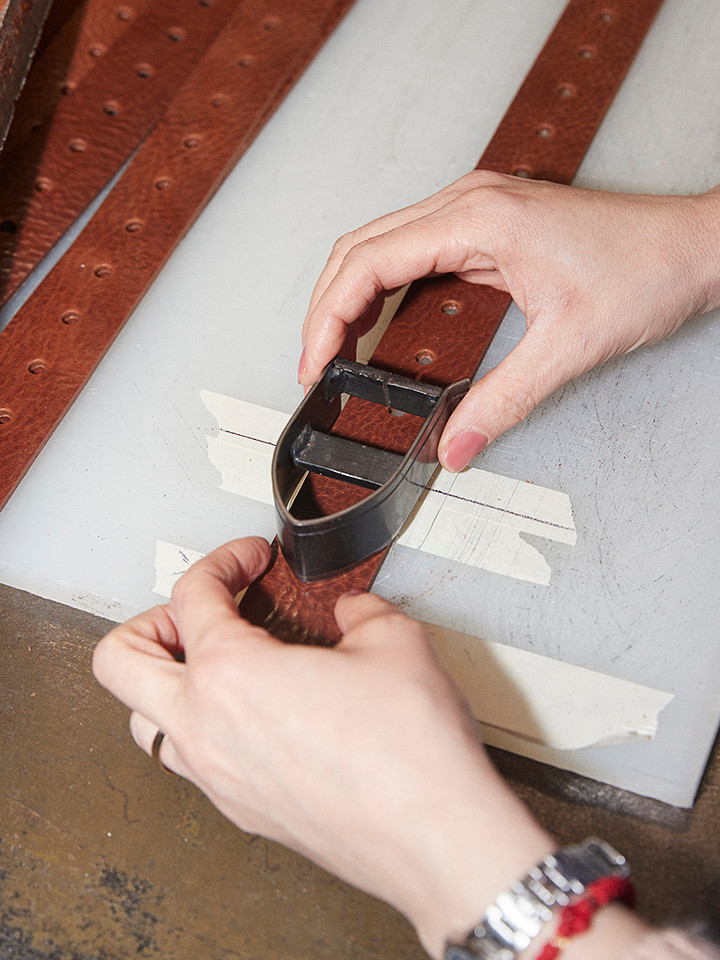
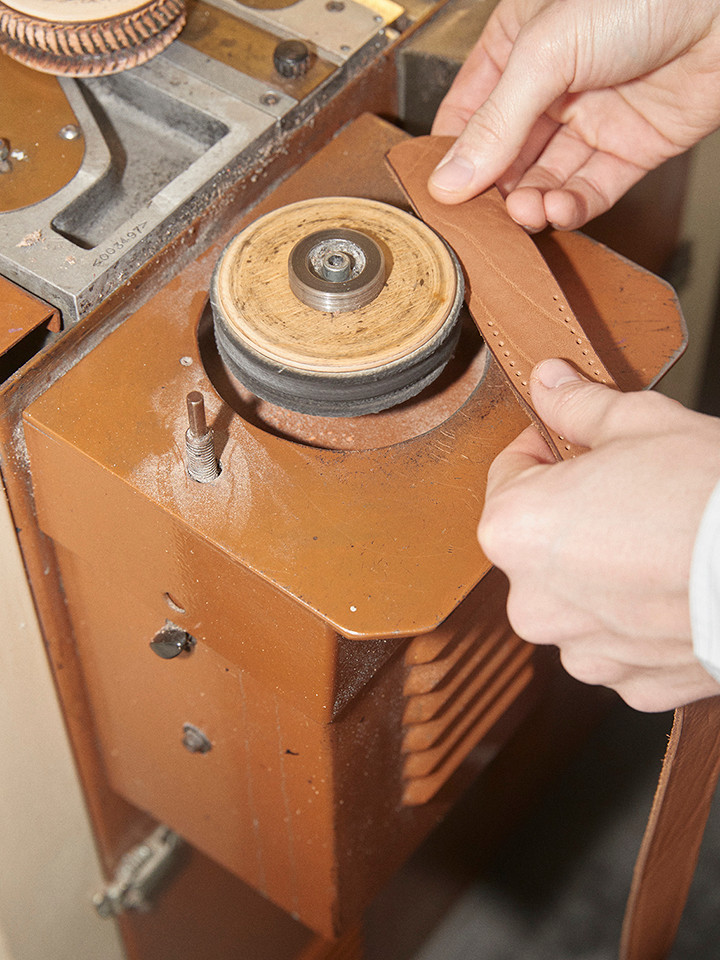
Interview by Giulia Stanzione, Text by Laura Reinke, Photography by Maximilian Attila Bartsch
Every pair of Closed jeans is 100% Made in Italy – and we mean it! Even the brass buttons and rivets for our jeans are crafted in Italy – in the Cobrax button factory in Padova, to be precise. While high-tech equipment and robots are also used, the 177 employees also complete many production steps by hand under high safety standards. They punch out the individual button components from brass strips, emboss our logo on them, polish and assemble them into a finished button. Most of the buttons are then coated or treated with chemical solutions to achieve specific colours. All brass scraps are collected, melted down and reused. Since 2008, Cobrax has been part of the Riri Group, a leading international manufacturer of zips, (press) buttons, rivets and metal components. We have been working with the company for more than 20 years now – and no Closed jeans would be truly complete without at least one of their beautiful buttons.
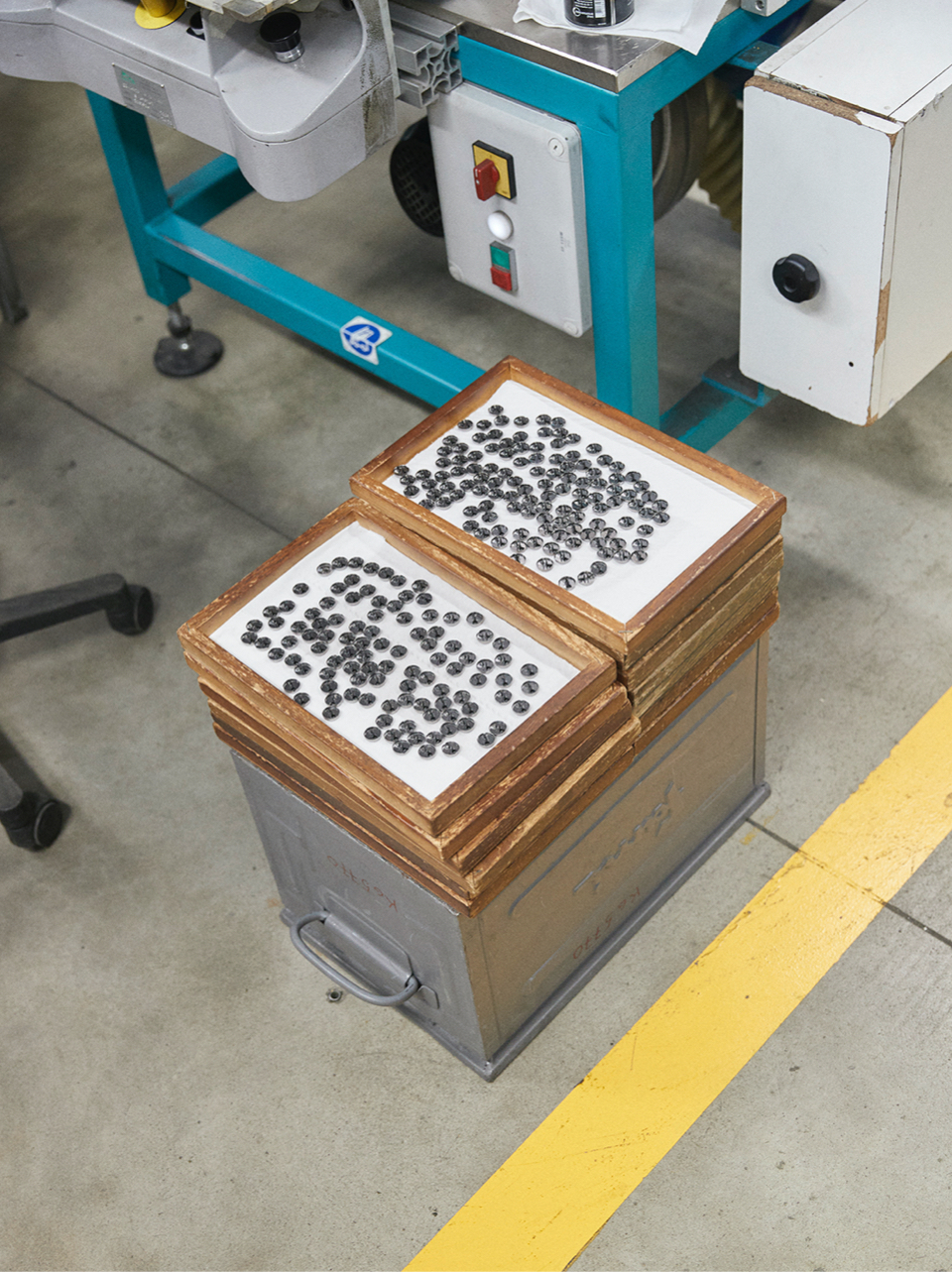
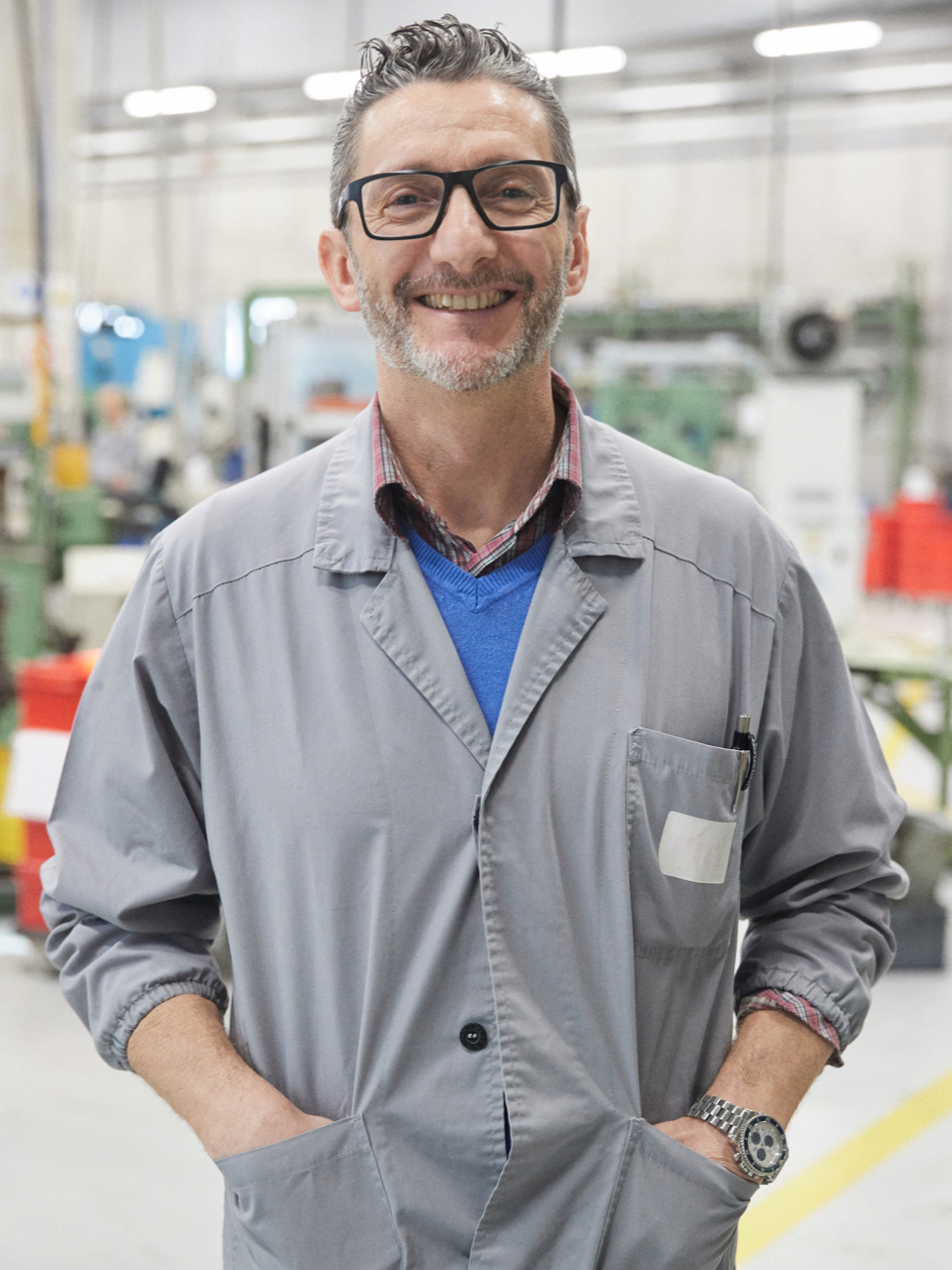
Andrea Norido joined Cobrax (then called Micron) in 1986. Back then, the company only had 14 employees. Andrea learned everything from scratch. Today, he manages the printing department – and loves the technical aspect of his job.
How a button is made –
step by step
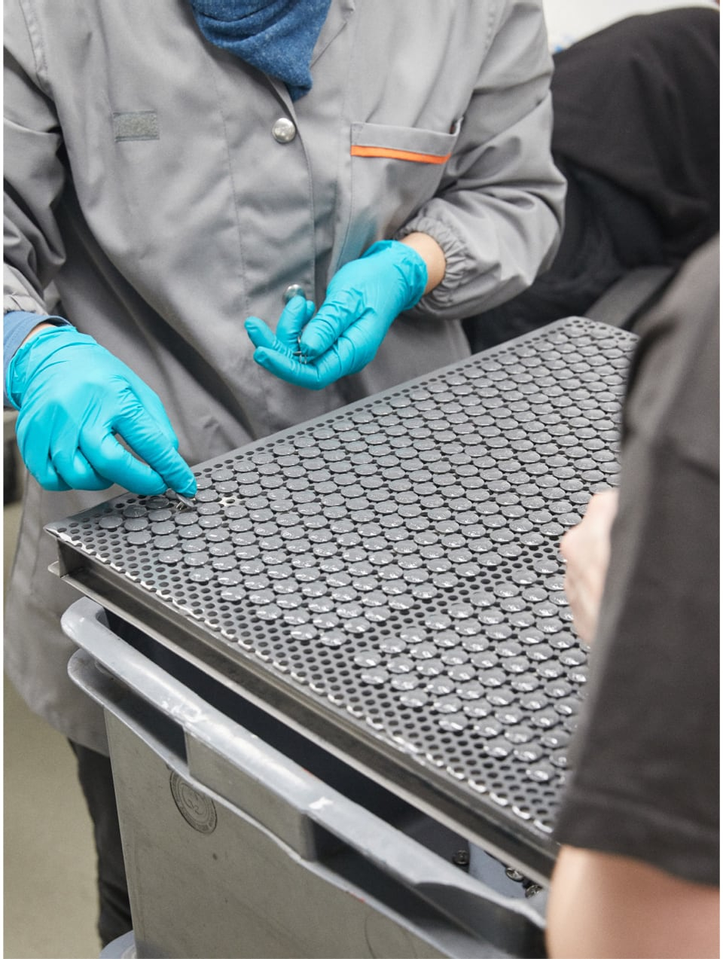
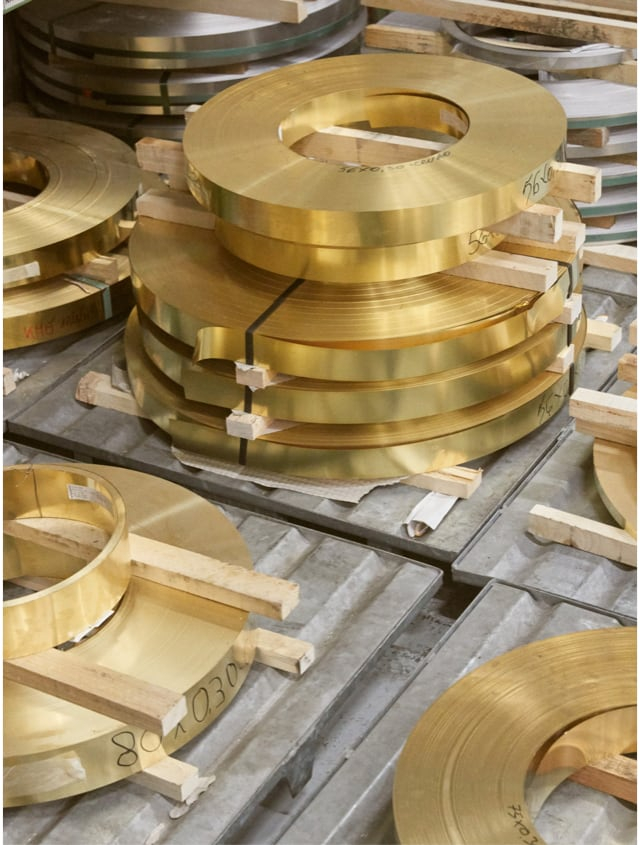
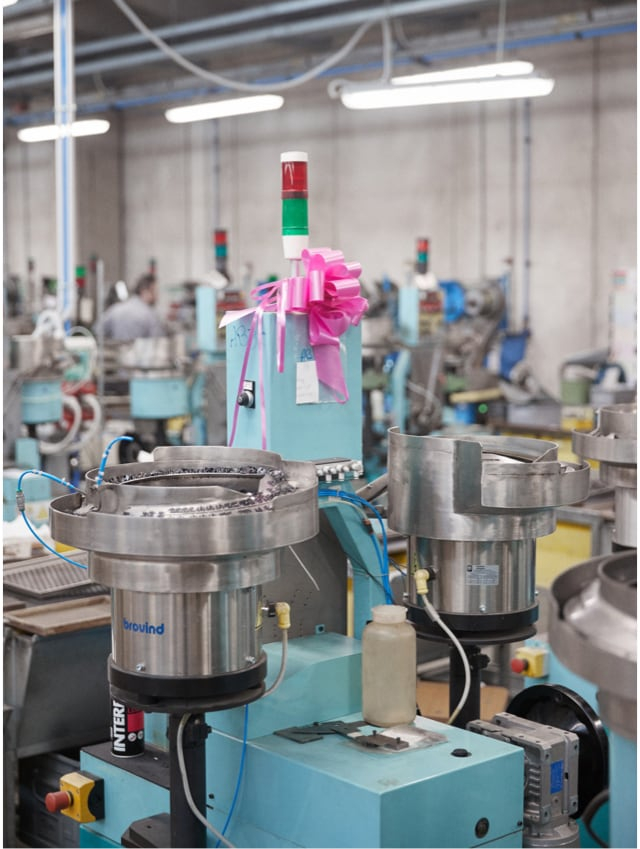
Interview and text by Laura Reinke, Photography by Maximilian Attila Bartsch
Our leather bags are made in Portugal, exclusively by our long-standing production partner, Daro’s. The family business with 187 employees has been manufacturing our bags and leather acces sories since 2013. The company’s headquarters in São Pedro da Cova near Porto may look futuristic, but everything here is about traditional craftsmanship: many steps of the production process are done by hand. Daro’s uses vegetable tanned leather – which means it has been treated using low-impact processes that are gentler on the precious material and on the environ ment. The results are long-lasting, high-quality bags that become even more beautiful with time.
The company was founded in 1972. Shortly after the birth of her daughter Carla, Celeste Oliveira Soares set up her own leather goods business. Her husband David Roque joined in 1981 (Daro’s is a play on the letters of both names). Carla manages the company today, while her brother Paulo is in charge of material purchasing and finances. The third generation, granddaughter Ines, also started at the company a while ago.
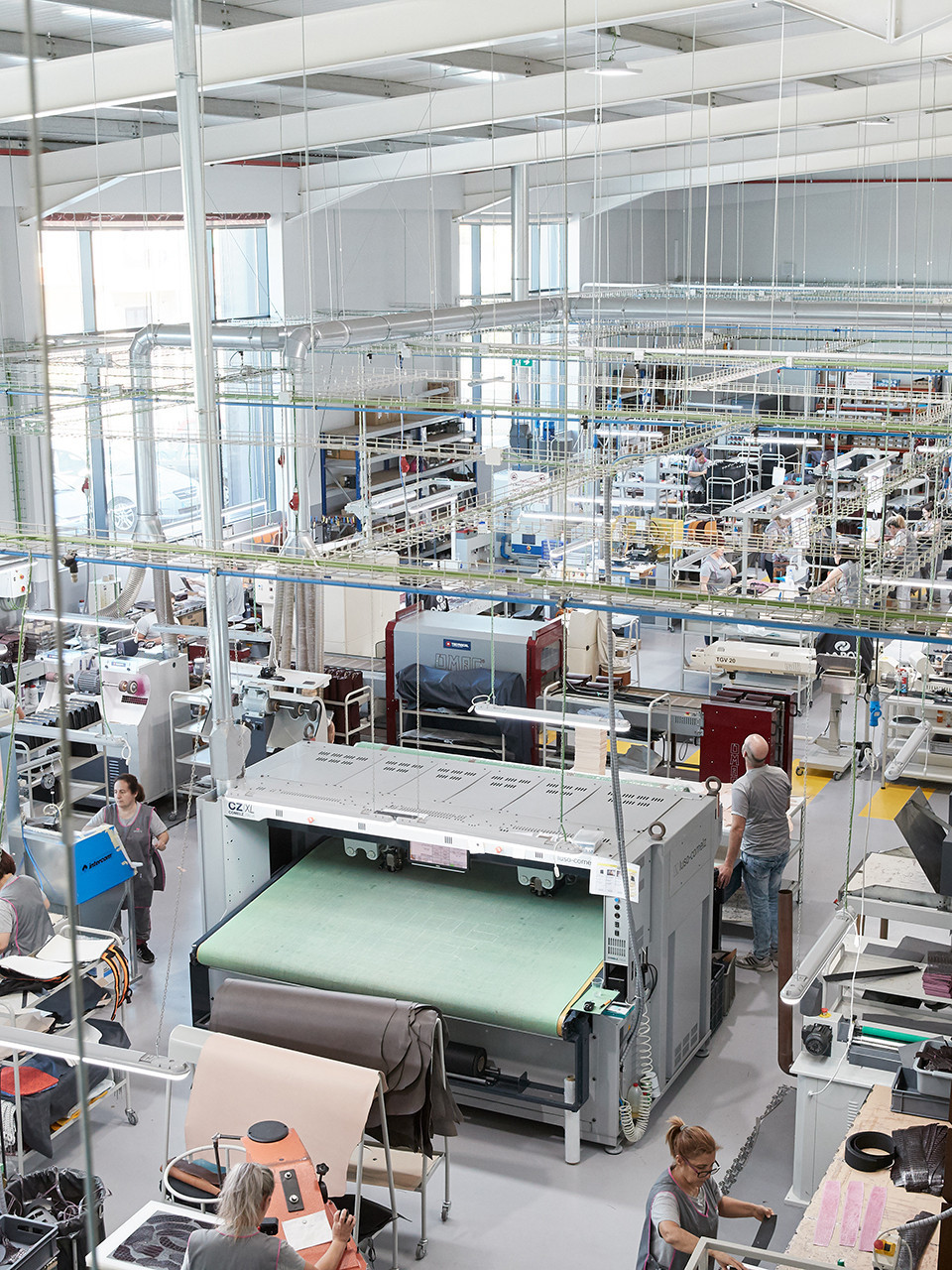
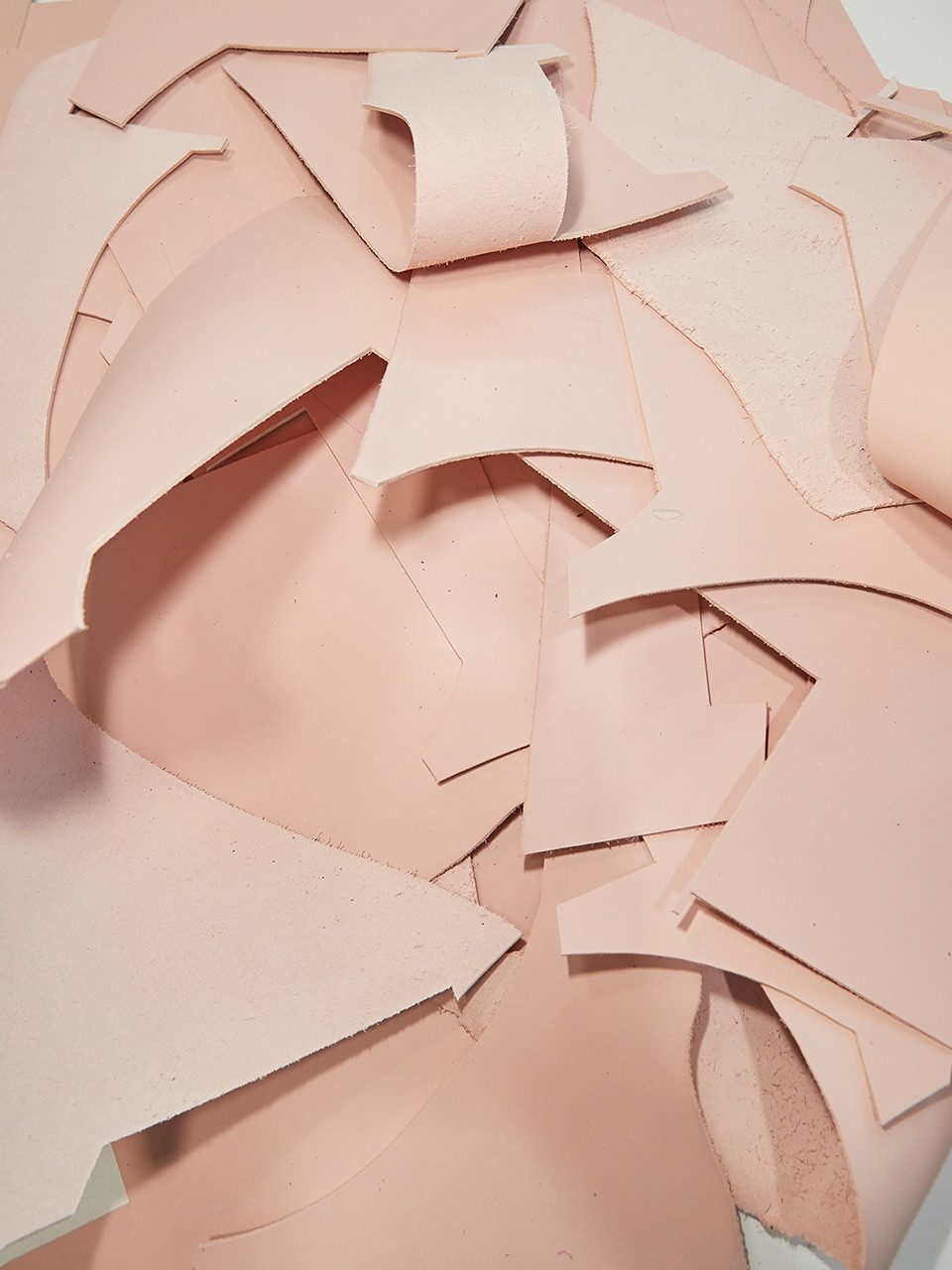
We spoke to Carla, who joined her parents’ company 32 years ago, to tell us about a typical day at Daro’s – and to show us how a Closed leather bag is made step by step.
How a bag is made –
step by step
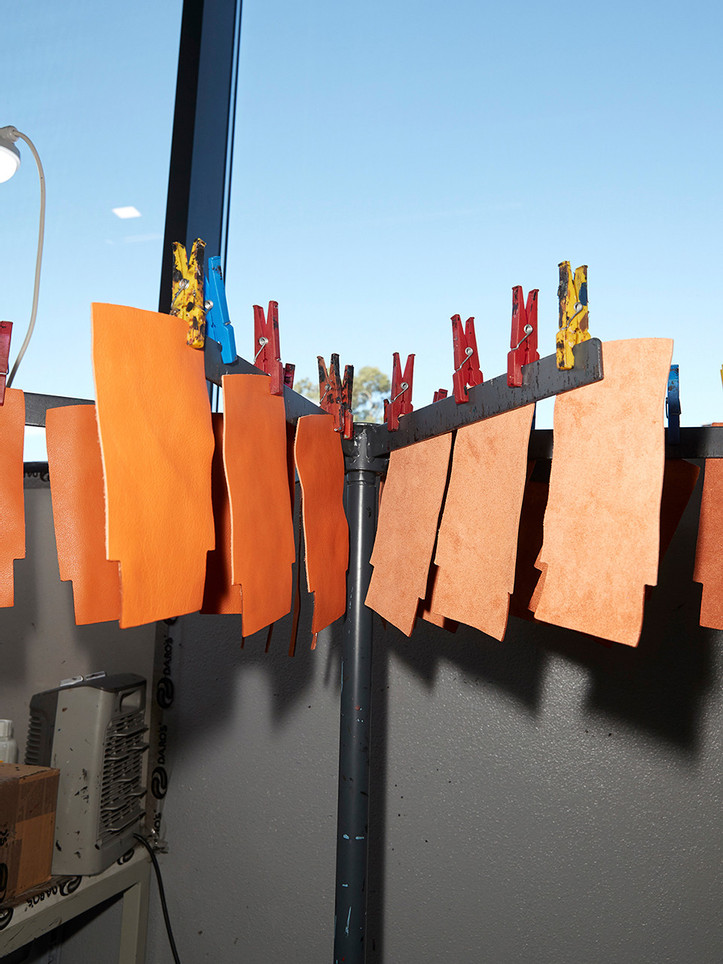
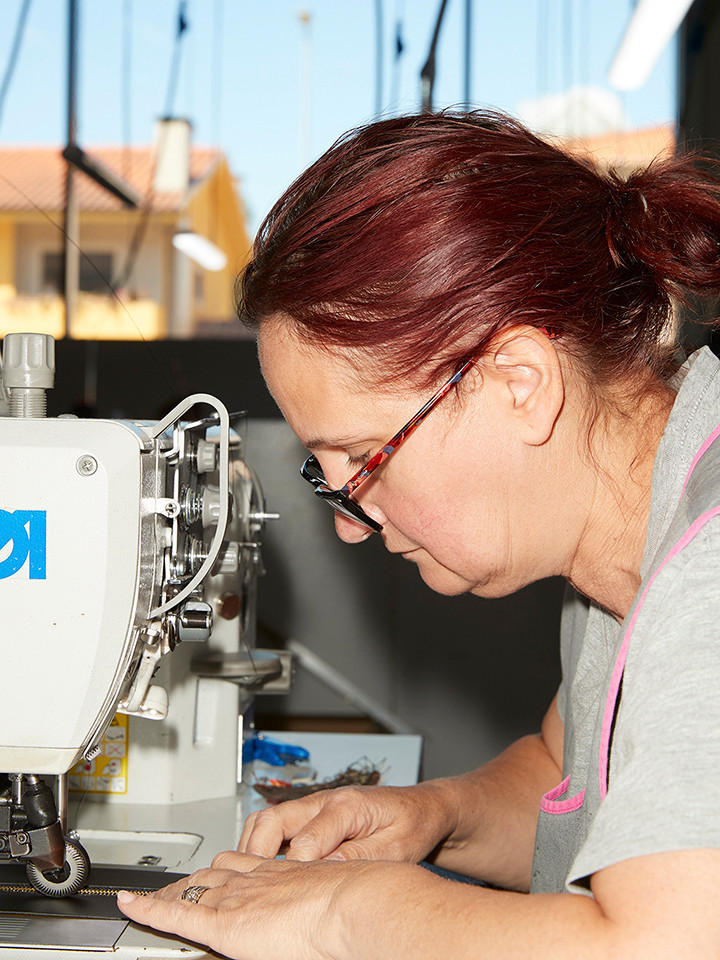
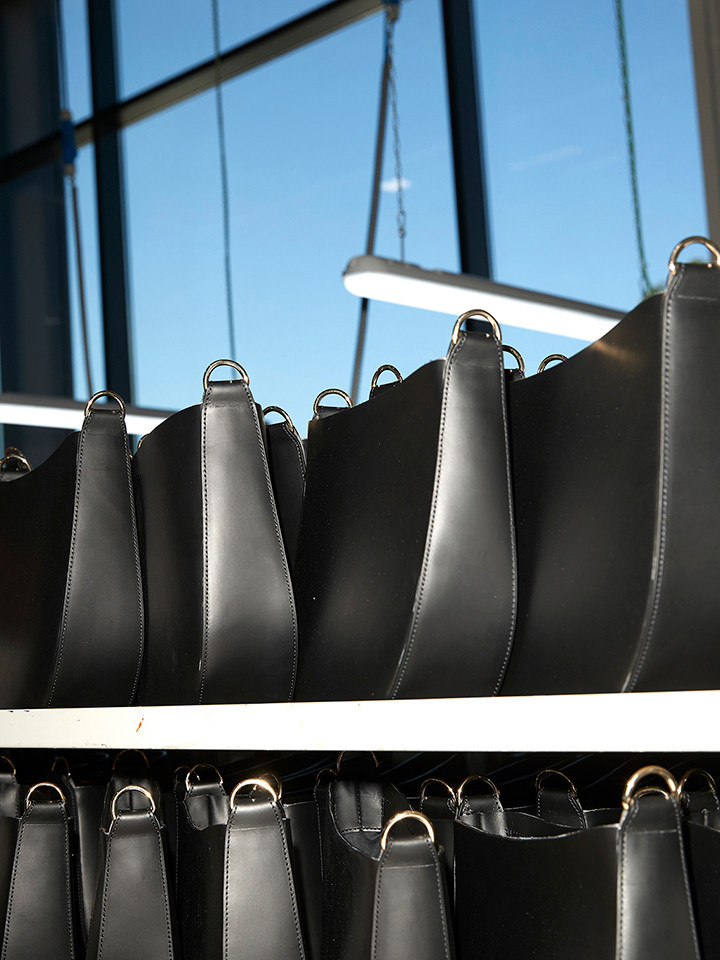
Past Stories
Copy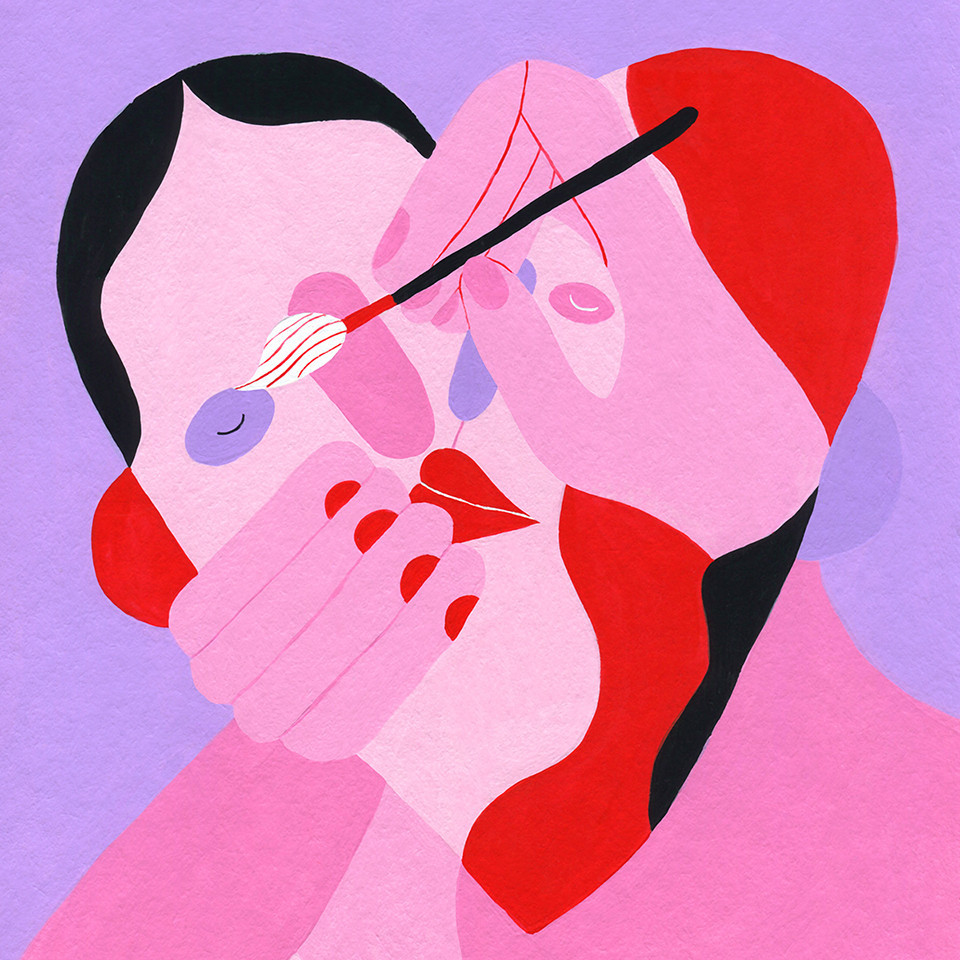